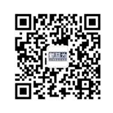
微信公眾號二維碼
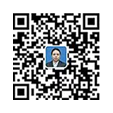
微信咨詢顧問二維碼
新益為精益生產(chǎn)咨詢公司概述:精益生產(chǎn)(Lean Production,簡稱LP),精益生產(chǎn)是起源于日本豐田汽車公司的一種生產(chǎn)管理方式。第二次世界大戰(zhàn)后,日本汽車工業(yè)開始起步,但此時統(tǒng)治世界的生產(chǎn)模式是以美國福特制為代表的大量生產(chǎn)方式。
精益生產(chǎn)咨詢
生產(chǎn)制造管理中的成本控制是生產(chǎn)管理的重要組成部分。在“生產(chǎn)成本五三模型”中,三大無形成本的核心內(nèi)容是七大浪費。七大浪費最早由豐田企業(yè)提出。并且可以在制造管理中應用和改進。
大野耐一將大規(guī)模制造方法的浪費分為七大類:(1)等待浪費;(2)搬運浪費;(3)不良品的浪費;(4)動作的浪費;(5)加工浪費;(6)庫存的浪費;(7)制造過多浪費。
1、庫存浪費
庫存的主要原因是:管理者為了自己工作的方便或該區(qū)域生產(chǎn)的定量控制而分批下單,而不是結(jié)合主生產(chǎn)計劃的要求,流線型生產(chǎn)導致局部大批量庫存。
庫存損壞表現(xiàn)包括:
(1)產(chǎn)生不必要的運輸、堆積、放置、防護處理、搜索等廢棄物。
(2)使先進先出變得困難。
(3)利息和管理成本的損失。
(4)物品的價值會降低,成為滯銷物品。
(5)占用廠房空間,造成多余廠房及倉庫建設(shè)投資的浪費。
(6)無管理的緊張阻礙了改進。
(7)對裝備能力和人員需求的誤判。
2、生產(chǎn)過剩的浪費
指生產(chǎn)的產(chǎn)品多于下一道工序或客戶的需求,或過早生產(chǎn)。
生產(chǎn)過剩的主要原因是:產(chǎn)能不足,生產(chǎn)過程不穩(wěn)定,管理人員認為過度生產(chǎn)和過早生產(chǎn)可以提高效率,減少生產(chǎn)損失,平衡車間生產(chǎn)力。
制造過多損害表現(xiàn)是:
(1)支出(材料成本、人工成本)早,不能創(chuàng)造利潤。
(2)隱藏“等待的浪費”,使管理者忽視等待的發(fā)生和存在。
(3)產(chǎn)品積壓,不僅會使加工時間變長,還會使現(xiàn)場工作的空間變大,機器之間的距離會拉大,逐漸蠶食利潤。
(4)運輸和堆積的浪費使先進先出操作困難。
3、搬運浪費
不必要的零件和產(chǎn)品處理,例如兩個連續(xù)的生產(chǎn)過程。完成一個工序后,產(chǎn)品先運到倉庫,再運到下一道工序。理想的情況是讓兩道工序位置相鄰,使產(chǎn)品可以立即從一道工序轉(zhuǎn)移到下一道工序。
處理的主要原因是:車間布局采用批量生產(chǎn),集中橫向布局以工作站區(qū)分,沒有連續(xù)流生產(chǎn)的概念。
4、等待的浪費
在生產(chǎn)過程中,操作人員或設(shè)備處于閑置狀態(tài)。
等待原因主要有:操作不平衡、操作安排不當、等待材料、質(zhì)量差等。
5、多余動作的浪費
操作員不增值的操作,例如查找零件、工具、文件等。
造成重復動作的主要原因有:生產(chǎn)場地規(guī)劃不善、生產(chǎn)模式設(shè)計不完善、生產(chǎn)動作不規(guī)范。
6、缺陷的浪費
不良品和廢品。
造成缺陷的主要原因是:過程生產(chǎn)中沒有標準確認或標準確認沒有與標準操作相比較,管理不嚴格和松懈。
7、過度加工的浪費
加工程度超出客戶需要或不必要的修正加工。
過度加工的主要原因是:制造過程中加工程序的運行沒有得到優(yōu)化,可省略、替代、重組或合并的未及時進行改善。
精益生產(chǎn)如何解決生產(chǎn)浪費呢?以上就是新益為精益生產(chǎn)咨詢公司的相關(guān)介紹,做好企業(yè)的精益管理工作就是為精益生產(chǎn)管理活動打下基礎(chǔ),讓精益生產(chǎn)管理在企業(yè)中發(fā)展有一個良好的前提。
建立生產(chǎn)有序、管理順暢,操作規(guī)范,士氣高昂、高質(zhì)量、低成本、短交期的作業(yè)現(xiàn)場;
為企業(yè)規(guī)劃設(shè)計一套由內(nèi)到外的形象升級,外觀視覺價值體現(xiàn)、內(nèi)在的管理內(nèi)涵體現(xiàn);
全員參與設(shè)備管理高產(chǎn)出和低成本運營,提升設(shè)備管理能力,維護能力,提高效率
構(gòu)建班組生產(chǎn)管理體系、循環(huán)評價、人才育成、持續(xù)改善、績效管理、文化養(yǎng)成體系;
提高產(chǎn)品質(zhì)量、降低生產(chǎn)成本、縮短交期、增加利潤,讓管理更系統(tǒng)科學,執(zhí)行力更強
對工廠的各個組成部分進行合理安排,以提高生產(chǎn)效率、降低成本、優(yōu)化物流、改善工作環(huán)境等