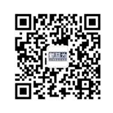
微信公眾號二維碼
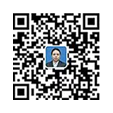
微信咨詢顧問二維碼
精益生產咨詢公司概述:單件流生產是精益生產中一個非常重要的概念,是準時化生產的核心,能夠實現生產流整體效益的平衡,是消除浪費的最好方法。與傳統的批量生產相比,單件流的生產的優(yōu)勢有哪些呢?
單件流生產
一、在保證質量的同時,縮短生產周期
產品生產常由多工序組成,企業(yè)一般按分工原則將產品生產工序分給多個工位,分工降低了工作難度,提高了作業(yè)效率,但分工對生產組織增加了難度,只有各工位有效配合,才能保障整體的產出和效率。
傳統批量流動生產方式的弊病,突出表現形式為各工位工人各顧各大批量生產,忙于各自工序生產任務而不關心在制品流轉和整體產出,結果生產周期大大拉長。
單件流生產同樣采取分工原則,但要求各工序不是批量生產后再流轉下工位,而是生產一件(是否一件最高效最經濟需結合具體行業(yè),以設定標準)就要流轉下工位,精益生產并要求各工位按統一節(jié)拍生產,以實現生產過程順暢,在制品不積壓,按此種方式能快速得到成品,根據節(jié)拍和生產工時就可得知完成產量所需總周期,根據目標差異就可靈活應對,保障交貨及時。
二、連續(xù)流動生產,有效減少在制品數量
傳統生產是大批量生產,即各工位各自的大批量生產,必然結果是各工位均有大量在制品。精益生產單件流生產是連續(xù)流動生產,突出特點是在制品得以極大的壓縮。
三、減少在制品的同時,增加了空間利用率
單件流生產極大的削減了在制品,工廠空間得以解放。在一些企業(yè),在制品占地面積僅次于設備占地面積,在制品區(qū)域很大卻還不夠用,通道上也放置在制品。此類企業(yè)推行精益生產的要點之一是推行連續(xù)流動生產,突出收益是削減在制品、減少在制品場地占用,增加空間利用率。
四、產品生產過程中靈活性大
傳統大批量生產方式,在生產現場投入了大量資金,各工位有大量的在制品,生產周期長。一旦出現生產異常,就影響正常產出和交貨。一旦客戶需求量減少,就會造成大量積壓。而若客戶提出其他產品品種需求時,因車間內已有大量在產品,企業(yè)要么選擇在制品下線暫停,以便新品種正常投產,要么選擇加班加點干完原有產品后再生產新品種。不論何種選擇,要么是前者造成在制品積壓,要么是后者造成產成品積壓,對企業(yè)來說都不愿看到。
單件流生產方式,企業(yè)在制品總量極少,原材料的投入短周期內就轉化為成品,對于客戶需求變化的應對能力均大大提高,對于不同產品品種轉換時間能大幅削減。以某服裝企業(yè)為例,推行精益生產前,品種轉換通常需24小時,按一天8小時生產時間計,需三個工作日才能實現換產,推行精益生產后,品種轉換按各線正常生產流程投料即可,即上一品種正常生產結束,下一品隨后按節(jié)拍就能出成品,對于有些產品差異大需調配機器或換線清臺等,常在30分鐘內也能完成品種轉換。
單件流生產對生產組織和相關配套服務工作要求高,在推行單件流生產中,完善了相關工作要求和職責,解決了大量生產異常問題,提高了相關人員的技能和責任心,相對批量生產反倒大量降低了生產異常對生產造成的影響和損失。此種生產狀態(tài)使企業(yè)應變能力大為增強。
五、質量管理上,有效減少產品質量缺陷
傳統大批量生產方式,各工位工人各顧各大批量生產,在質量管理上增加了數倍的難度。由于各工位工人都有大批量在制品產出,單靠自我質量保障顯然不可靠,及時的互檢在此生產方式下不現實,只有靠專檢,靠檢驗員或班長進行質量把關。這樣,質檢員和班長將面臨所有工位的質量檢驗任務,工作量巨大。即使質檢員和班長很盡力,在生產中輪番對各工位產品進行檢查,質量風險仍舊很大。經常出現的情況是,難以發(fā)現質量異常,而若發(fā)現了某工序的質量異常,則極可能已是批量質量事故。
六、工人自檢,能快速發(fā)現缺陷并及時糾正
相比較,單件流生產能快速出成品,各工位生產是有序銜接按節(jié)拍的,工人的自檢是能實現的一項質量保障的基礎工作,而下工序的互檢則相對較容易實現,質檢員和班長的專檢則要輕松很多,能迅速對最終產品進行檢驗,及時發(fā)現各工序存在的質量問題,及時進行糾正,能有效避免批量質量缺陷。
建立生產有序、管理順暢,操作規(guī)范,士氣高昂、高質量、低成本、短交期的作業(yè)現場;
為企業(yè)規(guī)劃設計一套由內到外的形象升級,外觀視覺價值體現、內在的管理內涵體現;
全員參與設備管理高產出和低成本運營,提升設備管理能力,維護能力,提高效率
構建班組生產管理體系、循環(huán)評價、人才育成、持續(xù)改善、績效管理、文化養(yǎng)成體系;
提高產品質量、降低生產成本、縮短交期、增加利潤,讓管理更系統科學,執(zhí)行力更強
對工廠的各個組成部分進行合理安排,以提高生產效率、降低成本、優(yōu)化物流、改善工作環(huán)境等