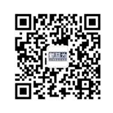
微信公眾號二維碼
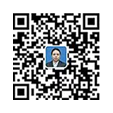
微信咨詢顧問二維碼
新益為精益管理咨詢公司概述:準(zhǔn)時化生產(chǎn)JIT(Just In Time)是根據(jù)豐田喜一郎的構(gòu)想發(fā) 展而來的,早在1936年豐田自動紡織機制作所汽車部正式開始生產(chǎn)的時候,豐田喜一郎在工廠里貼上一張寫著Just In Time的標(biāo)語,并在1938年舉母工廠竣工的時候,編寫了詳細(xì)的小冊,這是為了更加徹底實行Just In Time工作辦法。所謂JIT(Just In Time)就是”在必要的時間生產(chǎn)或者搬運必要數(shù)量的必要的產(chǎn)品”的狀態(tài)。從1947年以后,大野耐一開動腦筋絞盡腦汁想出各種解決辦法(逆向思維打破常規(guī)和習(xí)慣),按照自己設(shè)計的必要條件,分階段地進(jìn)行實驗,逐漸形成一完整的體系。這里的必要條件包括以下幾方面。
準(zhǔn)時化生產(chǎn)
1、機械車間首先建立生產(chǎn)流水線
1947年大野耐一擔(dān)任舉母工廠第二機械制作長主任就開始改善,把機器排成“二字形”或者“L字形”,試行一個操作員管理兩臺設(shè)備,在1949年改為“口字形”或者“U字形”,并管理不同工序的三臺設(shè)備或者四臺設(shè)備,實現(xiàn)按照加工工序來搭配安排不同的設(shè)備,一個一個加工制造,也就是機械車間流水線單件作業(yè)。
2、逆向思維,后工序領(lǐng)取方式
JustInTime是一一種具有很多優(yōu)點的管理方式,怎樣才能做到“JIT準(zhǔn)時化”,大野耐一利用逆向思維把事物倒過來思考。如果由后一道工序在必要的時刻向前一道工序領(lǐng)取必要數(shù)量的必要產(chǎn)品,然后前一道工序只要生產(chǎn)被領(lǐng)取數(shù)量的產(chǎn)品,這樣明確提出了“某種產(chǎn)品需要領(lǐng)取多少和某種產(chǎn)品需要生產(chǎn)多少”,也就可以把許多道分割開的工序連續(xù)在一起,也就可以滿足非常準(zhǔn)時的Just in Time的要求,這就是后工序領(lǐng)取方式。
最后的裝配線去向前一一道工序領(lǐng)取要用的各種零件,前一道工序被領(lǐng)取零件后重新生產(chǎn)被領(lǐng)取的零件,就可以把生產(chǎn)工序一直往前追溯,直到原材料供應(yīng)商都同步運行起來。后工序領(lǐng)取方式從1948年開始實施,1949年廢除了中間倉庫。
3、均衡生產(chǎn)
在機械車間和總裝車間聯(lián)系起來實現(xiàn)同步運行后,為了使工作速度一致,在1950年總裝車間開始了均衡生產(chǎn)(把每日的生產(chǎn)量平均化)。
4、拉動看板
1953年公司的機械工廠開始試行并實際應(yīng)用拉動看板。拉動看板成為了豐田汽車公司內(nèi)部以及豐田汽車公司用供應(yīng)商之間相互傳遞信息,起到上下協(xié)同聯(lián)系的作業(yè)。拉動看板就是一個表明零件(部件)型號以及其他生產(chǎn)所必須了解事項的紙片,單單一張看板就可以一目了然地了解生產(chǎn)時間、生產(chǎn)方式、生產(chǎn)數(shù)量、搬運時間、搬運地點、搬運方式、容器等相關(guān)信息。
眾所周知大野耐一在受美國超市啟迪開始了拉動看板生產(chǎn)方式。到了1962年豐田汽車公司所有公司都采用了拉動看板方式,用看板把機械鍛造熱處理鑄件車體一總裝車間都連接了起來。供應(yīng)商從1965年開始采用看板, 1982年豐田公司將外協(xié)訂貨看板應(yīng)用到了98%的供應(yīng)商廠家。
Just In Time貫穿了整個豐田生產(chǎn)方式的建立過程,1947年以后開始在機械車間流水線生產(chǎn)直至1980年拉動看板形成,為世人熟悉。只有單件流生產(chǎn),才有可能在極短的時間將內(nèi)制造出產(chǎn)品,從而滿足客戶的需要。而均衡生產(chǎn)條件下按照節(jié)拍來生產(chǎn)則可以將生產(chǎn)的時間留給客戶需要的產(chǎn)品而不是制造庫存,以及最后用拉動看板將各個分開的工序連接起來,最后形成Just In Tim生產(chǎn)方式和為人所熟知的豐田生產(chǎn)方式。
現(xiàn)如今拉動看板依然貫穿在整個豐田生產(chǎn)運作過程中, 豐田供應(yīng)商零件采購、工序間半成品、裝配、集貨、帶包和配送需要看板,在保有極少的庫存情況下每天按照不同的送貨頻次送貨給豐田汽車總裝車間需要看板,在汽車總裝車間不同類型的零部件通過P一lane、PC棚、SPS中轉(zhuǎn)、儲存、分揀需要用到看板,不同車型不同零部件被送到不同工位上需要用到看板,而工位上需要生產(chǎn)什么車型也是通過看板來進(jìn)行控制??窗逑褚粋€個齒輪咬合、 控制、驅(qū)動每個功能模塊來達(dá)到用最少的庫存在最短的時間以同步化方式嚴(yán)格按照客戶需要的數(shù)量、需要品種和需要時間交給客戶。這個復(fù)雜的系統(tǒng)能精巧、穩(wěn)定、精確和細(xì)致地運作,拉動看板起到了很了不起的作用。
拉動看板在國內(nèi)應(yīng)用時存在一些誤區(qū):第一種情況,僅僅把看板當(dāng)作降低庫存的工具,在這種應(yīng)用條件下,往往庫存降低到一定的數(shù)值就停止了,而看板成為維持庫存水平的手段,沒有起到通過拉動看板不斷進(jìn)行錘煉改善團隊、提升企業(yè)經(jīng)營體質(zhì)的作用。
第二種情況,在企業(yè)的部分流程中運作看板,而不是全公司全流程運作看板。這種情況看板僅局限于生產(chǎn)制造的某一個環(huán)節(jié),如出現(xiàn)供應(yīng)商跟原材料庫存拉動,僅在生產(chǎn)前后工序間的物料拉動環(huán)節(jié)。這種有推有拉的方式,最終得到的只是看板部分功能作業(yè)發(fā)揮。全流程運作看板拉動包括客戶接單、工序間指令生產(chǎn)、原材料購買、成品裝配、理貨配送整個環(huán)節(jié)。
第三種情況,粗暴式拉動看板。在沒有充分改善和均衡生產(chǎn)的條件下強制實施看板,沒有幫助供應(yīng)商進(jìn)行改善,強制要求按照看板準(zhǔn)時交貨,不考慮供應(yīng)商送貨成本,強制提高送貨頻率,沒有考慮供應(yīng)商庫存情況而強調(diào)自己庫存數(shù)量減少。在以自我為中心的看板運作下面,造成人們對看板的錯誤認(rèn)識,認(rèn)為看板僅是達(dá)到自利目的的工具而已。
作為JIT(Just In Time)中重要工具之一的拉動看板 ,在豐田汽車公司發(fā)揮著神奇和驚艷的效果,甚至有段時間被錯誤地當(dāng)作豐田生產(chǎn)方式的全部。而現(xiàn)今我國企業(yè)中運作拉動看板的效果并不理想,需要更多精益人士更深刻地學(xué)習(xí)、理解、實踐、體會、研究拉動看板應(yīng)用。
建立生產(chǎn)有序、管理順暢,操作規(guī)范,士氣高昂、高質(zhì)量、低成本、短交期的作業(yè)現(xiàn)場;
為企業(yè)規(guī)劃設(shè)計一套由內(nèi)到外的形象升級,外觀視覺價值體現(xiàn)、內(nèi)在的管理內(nèi)涵體現(xiàn);
全員參與設(shè)備管理高產(chǎn)出和低成本運營,提升設(shè)備管理能力,維護(hù)能力,提高效率
構(gòu)建班組生產(chǎn)管理體系、循環(huán)評價、人才育成、持續(xù)改善、績效管理、文化養(yǎng)成體系;
提高產(chǎn)品質(zhì)量、降低生產(chǎn)成本、縮短交期、增加利潤,讓管理更系統(tǒng)科學(xué),執(zhí)行力更強
對工廠的各個組成部分進(jìn)行合理安排,以提高生產(chǎn)效率、降低成本、優(yōu)化物流、改善工作環(huán)境等