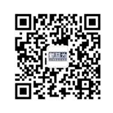
微信公眾號二維碼
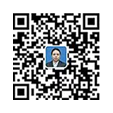
微信咨詢顧問二維碼
新益為精益生產(chǎn)咨詢公司概述:想要打敗敵人必先了解敵人,對于車間現(xiàn)場管理來講,浪費恐怕是最大的敵人。因為浪費,企業(yè)付出了高額的生產(chǎn)成本還毫不知情;因為浪費,本來2個人能完成的工作偏偏需要5個人;因為浪費,企業(yè)付出大量的人力成本。
凡是不能創(chuàng)造價值的活動都稱之為浪費,想要消除車間現(xiàn)場管理中的浪費,一定要認識這八項浪費現(xiàn)象。
精益生產(chǎn)之消除八大浪費
一、八大浪費
1、車間現(xiàn)場管理八項浪費之一:不良、修理的浪費
所謂不良、修理的浪費,指的是由于工廠內(nèi)出現(xiàn)不良品,需要進行處置的時間、人力、物力上的浪費,以及由此造成的相關損失。
這類浪費具體包括:材料的損失、不良品變成廢品;設備、人員和工時的損失;額外的修復、鑒別、追加檢查的損失;有時需要降價處理產(chǎn)品,或者由于耽誤出貨而導致工廠信譽的下降。
2、車間現(xiàn)場管理八項浪費之二:加工的浪費
加工的浪費也叫過分加工的浪費,主要包含兩層含義:
第一是多余的加工和過分精確的加工,例如實際加工精度過高造成資源浪費;第二是需要多余的作業(yè)時間和輔助設備,還要增加生產(chǎn)用電、氣壓、油等能源的浪費,另外還增加了管理的工時。
3、車間現(xiàn)場管理八項浪費之三:動作的浪費
動作的浪費現(xiàn)象在很多企業(yè)的生產(chǎn)線中都存在,常見的動作浪費主要有以下12種:
兩手空閑、單手空閑、作業(yè)動作突然停止、作業(yè)動作過大、左右手交換、步行過多、轉(zhuǎn)身的角度太大,移動中變換“狀態(tài)”、不明技巧、伸背動作、彎腰動作以及重復動作和不必要的動作等等,這些動作的浪費造成了時間和體力上的不必要消耗。
4、車間現(xiàn)場管理八項浪費之四:搬運的浪費
從JIT的角度來看,搬運是一種不產(chǎn)生附加價值的動作,而不產(chǎn)生價值的工作都屬于浪費。
搬運的浪費具體表現(xiàn)為放置、堆積、移動、整列等動作浪費,由此而帶來物品移動所需空間的浪費、時間的浪費和人力工具的占用等不良后果。
國內(nèi)目前有不少企業(yè)管理者認為搬運是必要的,不是浪費。因此,很多人對搬運浪費視而不見,更談不上去消滅它。
也有一些企業(yè)利用傳送帶或機器搬運的方式來減少人工搬運,這種做法是花大錢來減少工人體力的消耗,實際上并沒有排除搬運本身的浪費。
5、車間現(xiàn)場管理八項浪費之五:庫存的浪費
按照過去的管理理念,人們認為庫存雖然是不好的東西,但卻是必要的。JIT的觀點認為,庫存是沒有必要的,甚至認為庫存是萬惡之源。
例如,有些企業(yè)生產(chǎn)線出現(xiàn)故障,造成停機、停線,但由于有庫存而不至于斷貨,這樣就將故障造成停機、停線的問題掩蓋住了,耽誤了故障的排除。
如果降低庫存,就能將上述問題徹底暴露于水平面,進而能夠逐步地解決這些庫存浪費。
6、車間現(xiàn)場管理八項浪費之六:制造過多過早的浪費
制造過多或過早,提前用掉了生產(chǎn)費用,不但沒有好處,還隱藏了由于等待所帶來的浪費,失去了持續(xù)改善的機會。
有些企業(yè)由于生產(chǎn)能力比較強大,為了不浪費生產(chǎn)能力而不中斷生產(chǎn),增加了在制品,使得制品周期變短、空間變大,還增加了搬運、堆積的浪費。
此外,制造過多或過早,會帶來龐大的庫存量,利息負擔增加,不可避免地增加了貶值的風險。
7、車間現(xiàn)場管理八項浪費之七:等待的浪費
由于生產(chǎn)原料供應中斷、作業(yè)不平衡和生產(chǎn)計劃安排不當?shù)仍蛟斐傻臒o事可做的等待,被稱為等待的浪費。
生產(chǎn)線上不同品種之間的切換,如果準備工作不夠充分,勢必造成等待的浪費;每天的工作量變動幅度過大,有時很忙,有時造成人員、設備閑置不用;上游的工序出現(xiàn)問題,導致下游工序無事可做。
此外,生產(chǎn)線勞逸不均等現(xiàn)象的存在,也是造成等待浪費的重要原因。
8、車間現(xiàn)場管理八項浪費之八:管理的浪費
管理浪費指的是問題發(fā)生以后,管理人員才采取相應的對策來進行補救而產(chǎn)生的額外浪費。
管理浪費是由于事先管理不到位而造成的問題,科學的管理應該是具有相當?shù)念A見性,有合理的規(guī)劃,并在事情的推進過程中加強管理、控制和反饋,這樣就可以在很大程度上減少管理浪費現(xiàn)象的發(fā)生。
以上我們就了解了車間現(xiàn)場管理中普遍存在的八項浪費,這僅僅是消除浪費“萬里長征”路上的第一步,接下來還需要識別工序中哪里存在浪費,然后使用合適的工具來消除已經(jīng)識別的特定浪費,最后是重復實施上述步驟,實施持續(xù)性改進措施。
二、十大利器
下面,本文總結了現(xiàn)場管理十大利器,接著跟大家分享。
現(xiàn)場管理千頭萬緒,基本要素卻只有三個:
人、物、場所;現(xiàn)場情況千變?nèi)f化,歸結起來只有“兩流”:物流和信息流;作為現(xiàn)場管理者-生產(chǎn)主管、車間主任、班組長,必須對這三要素和兩流作細致的分析和研究,從中發(fā)現(xiàn)問題、分析原因、找出解決問題的答案來。
簡單講來就是:
工藝流程查一查;平面圖上調(diào)一調(diào);生產(chǎn)線上算一算;動作分要素減一減;搬運時空壓一壓;人機效率提一提;關鍵路線縮一縮;現(xiàn)場環(huán)境變一變;目視管理看一看;問題根源找一找。
本文旨在為現(xiàn)場管理者提供一個對現(xiàn)場管理分析和創(chuàng)造的思路和工具,掌握了它,也許不花一分錢,就可以從科學管理中要效率和效益。
1、工藝流程查一查
描述一個過程的步驟和傳遞路線的圖示叫流程圖。它包括工作流程和工藝流程兩大類,但實質(zhì)是一樣的,用它可以將復雜的過程用形象的圖示來表示。
工藝流程或工作流程是一個單位工藝或工作的總路線,它形象反映了工藝或工作的程序、部門和工序的連接、判定或檢查后的處理程序,
到一個企業(yè)或一個部門查找問題,應該從流程開始,“順藤摸瓜”分析現(xiàn)有生產(chǎn)、工作的全過程,哪些工藝流程不合理,哪些地方出現(xiàn)了倒流,哪些地方出現(xiàn)了停頓,哪些工藝路線和環(huán)節(jié)可以取消、合并、簡化?
分析判斷流程圖每個環(huán)節(jié)是否處于受控狀態(tài)?
檢驗是否能起到把關作用?各部門橫向聯(lián)系是否到位?是否通暢?
是否需要構建或增加新的通路?由流程圖的各個環(huán)節(jié)及傳遞路線,分析現(xiàn)有各部門的工作職能是否到位,是否要對現(xiàn)有機構進行調(diào)整或重組?
有道是“框框、菱形加線條組成,但是運用起來是個寶,任你工序多復雜,透視清楚別想跑!加一加,嚴格把關更牢靠;通一通,部門職能不落空。
減一減,換來效率大提高,定一定,有規(guī)有矩不爭吵!”
2、平面圖上調(diào)一調(diào)
有些在建廠初期就沒有對工地布置和設備布置進行過精心設計,或是由于生產(chǎn)的不斷發(fā)展,設備的不斷添置,打亂了布局,或是由于產(chǎn)品結構的變化,
造成了廠房或設備布置不合理,從而使產(chǎn)品和工件在生產(chǎn)時運輸路線過長,這是每時每刻都在制造浪費的隱患,必須下決心改變。
在工藝流程圖上是看不到平面路線的,流程圖上一個箭頭實際可能走幾十米,所以還要進一步在平面布置圖上去找效益。
通過分析作業(yè)方式和設備、設施的配置,按生產(chǎn)流程的流動方向,有無重復路線和倒流情況,找出不合理的部分,合理調(diào)整和設計一種新的布局,來縮短工藝路線和操作者的行走距離,減少不必要的資源浪費。
有時,一臺設備的移動會帶來幾十米甚至上百米距離的節(jié)省。有時會節(jié)省出更多的空間。
3、流水線上算一算
生產(chǎn)線和流水線應該按照一致的節(jié)拍進行,生產(chǎn)才能均衡。有的企業(yè)生產(chǎn)常常出現(xiàn)“前面干,后面看,前面提前走,后面在加班”的局面。
造成的原因一個是移動方式不合理,另一個就是節(jié)拍不均衡。
如果采用順序移動方式,每干完一批活以后再移到下一個工序,這就會造成下工序的等待和窩工。
如果以平行移動方式傳遞,即干好一個就往下工序傳遞一個,往往會使效率提高一倍。
一個由許多塊長短不同的木板箍成的木桶,決定其容量大小的并非其中最長的那塊木板,而是其中最短的那塊木板。
同樣,在流水線上,干得最慢的人就是決定流水線最終效率的人。生產(chǎn)線或流水線的平衡效率=各工序凈作業(yè)時間的總和/最長工序的作業(yè)時間×人員數(shù)。
很多生產(chǎn)流水線的平衡率常常不到50%,如果把時間長的工序通過簡化,提速、換人、或拆分的方法,對時間短的工序通過裁并、增加等等手法來平衡流水線。
整個生產(chǎn)線的生產(chǎn)效率就會大大提高,個別工序緩慢而導致的窩工和堆積就會消除。
4、動作要素減一減
任何操作都是以人工的動作為基本單元,特別是勞動密集型企業(yè),組裝工序、加工工序等這些以手工勞動為主體的工序,動作是產(chǎn)生效益的一個非常重要的因素。
進行動作分析,最主要的目的就是消除多余的動作、無效動作或緩慢動作,如彎腰作業(yè)、站在凳子上作業(yè)、蹲著作業(yè)、作業(yè)場所不暢、沒有適合的工位器具、人與物處于尋找狀態(tài)等,以最省力的方法實現(xiàn)最大的工作效率。
這個研究幾乎不花一分錢,就可以大大提高生產(chǎn)效率。例如在現(xiàn)實生活中,為什么有的人包餃子會比一般人快很多?
為什么有的人插秧會比一般人快很多?那都是因為他們掌握了一定的訣竅,以最經(jīng)濟的動作來完成任務。
試以包餃子為例,不少人會用八個以上的動作甚至幾十個動作來包一個餃子,如果你將勺子夾在右手小拇指上不放下來,按以下程序包餃子:左手拿皮子-右手挖餡放到皮子上-兩手合攏捏餃子成型-左手放餃子。
這樣,只要4個動作就可以包好餃子,效率比一般人提高一倍!
5、搬運時空壓一壓
據(jù)統(tǒng)計,加工費的25%到40%是搬運費;工序的時間,有70%到80%是搬運和停頓的時間;工廠的災害,又有85%是在搬運過程中發(fā)生的。
可見對搬運進行壓縮是非常重要的。改善搬運要對搬運進行優(yōu)化,從搬運數(shù)量、搬運空間、搬運時間上改善。
第一,要減少搬運的數(shù)量和搬運的次數(shù);
第二,在搬運空間上要盡可能縮短搬運距離、減少搬運路線和次數(shù);
第三,在搬運時間上要縮短時間、減少次數(shù);在方法上要注意管理協(xié)調(diào),盡量采用非動力如利用重力在斜坡滑行或在輸送帶上搬運。
搬運合理化的原則是要做到對被搬運物料幾乎無損耗;搬運方法要科學、文明、杜絕野蠻粗暴;搬運環(huán)境安全、適可、杜絕冒險;減少暫時放置現(xiàn)象的發(fā)生機會,盡可能做到一次到位;合理規(guī)劃工廠布局,可以有效縮短搬運距離。
在工廠規(guī)劃已經(jīng)定局時,通過合理化規(guī)劃流程,也可有效縮短搬運距離。
6、人機效率提一提
人和設備是一對矛盾,處理不好,就會發(fā)生不是人等機器就是機器等人。
人和設備構成了人機工程的關系,在分析時要分析作業(yè)者和機器在同一時間內(nèi)的工作情況,有無窩工、等待、無效時間,通過調(diào)整工作順序改進人機配合,尋求合理的方法,使人的操作和機器的運轉(zhuǎn)協(xié)調(diào)配合,將等待時間減少到最大限度,充分發(fā)揮人和機器的效率。就象擠水分一樣將互相等待的時間擠出去,這就是向人機聯(lián)合作業(yè)要效益。
7、關鍵路線縮一縮
幾乎任何一個產(chǎn)品都是由若干零件組成,通常要分幾條線或幾個工序生產(chǎn),而且到后期都要把零件一點一點組裝起來,在形成零件、部件過程中,不可避免地會發(fā)生各工序工作量大小不一的情況。
這就會在后期的生產(chǎn)中帶來互相制約,工作量小的工序的就會有很多空閑時間,而工作量大的工序就會沒有一刻休息時間,換句話說就是時差為零,成了生產(chǎn)上的瓶頸。
時差為零的工序就叫關鍵路線,它制約了企業(yè)或車間的產(chǎn)能和交貨期,我們在找出關鍵路線后,要從非關鍵路線上抽調(diào)人財物,加強關鍵路線,或采用平行作業(yè)、交叉作業(yè)等等形式,縮短關鍵路線,不斷修改和優(yōu)化計劃、達到縮短日程節(jié)省費用的最佳目標。
生產(chǎn)主管的基本功一是能根據(jù)計劃和生產(chǎn)能力推算和找出關鍵路線。二是不斷壓縮關鍵路線和其它路線,達到時間、費用的綜合優(yōu)化。這里有兩種方法:
第一種方法、時間優(yōu)化。就是在人力、設備、資金等有保證的條件下,尋求最短的工作周期。它可以爭取時間,迅速發(fā)揮投資效果。
利用時差,從非關鍵路線上抽調(diào)部分人力、物力集中用于關鍵路線,或分解作業(yè),增加作業(yè)之間的平行交叉程度,增加投入的人力和設備,采用新工藝,新技術來縮短關鍵路線的延續(xù)時間;
第二種方法,時間—費用優(yōu)化。工程項目的費用支出可以分為直接費用和間接費用兩部分。
直接費用是指與各項作業(yè)直接有關的費用如材料費、水電費,間接費用是指管理費用等不與各項活動直接有關,但隨時間變動而變動的費用,工程周期越短,間接費用越小。
時間—費用優(yōu)化就是尋求直接費用和間接費用之和最低時的工程周期。
8、場所環(huán)境變一變
分析生產(chǎn)、工作環(huán)境是否滿足生產(chǎn)、工作需要和人的生理需要,分析現(xiàn)場還缺少什么物品和媒介物,針對不同類別場所的問題,分別提出改進建議,
開展“整理、整頓、清掃、清潔、素養(yǎng)、安全”六項活動,做到永遠保持A狀態(tài),不斷改善B狀態(tài),隨時清除C狀態(tài),使員工保持旺盛的斗志和良好的技能,
所需物品隨手可取,不需要之物隨時得到清除,現(xiàn)場環(huán)境通暢、整潔、美化、安全、文明,使場所和環(huán)境在時間和空間上實現(xiàn)整體優(yōu)化。
9、目視管理看一看
人類大腦來自視覺方面的信息高達80%。因此用視覺來溝通和指揮的方法更為直接了當。
利用形象直觀、色彩適宜的各種視覺感知信息來組織現(xiàn)場生產(chǎn),以圖表、圖畫、照片、文字注解、標志、符號、作為目視管理的工具。
可以輕而易舉地達到解釋、認知、警告、判斷、行動等功能。所以目視管理也可稱之為“看得見的管理”、“可視化管理”。
10、問題根源找一找
每日尋找差距,以求第二天干得更好——這是海爾模式獨創(chuàng)性中非常重要的一點,不斷尋找問題、分析問題、永不休止地對現(xiàn)場進行改進,這是質(zhì)量改進、8D工作法、CIP等活動的共性。正是這一點推動著管理運作過程,使企業(yè)處于不斷向上的良性循環(huán)中。
這些現(xiàn)場改善的十大利器,如果你實實在在利用它,你就會發(fā)現(xiàn),這些利器神力非凡、所向披靡,你會驚喜地看到:
工藝路線順暢了、平面布置合理了,流水線上窩工消失了,節(jié)拍更均勻了、工人操作效率高了、搬運便捷了、生產(chǎn)均衡了、人機結合密切了,管理簡單了,一個更快、更好、更短、更順、更爽的精益生產(chǎn)局面已悄然降臨!
建立生產(chǎn)有序、管理順暢,操作規(guī)范,士氣高昂、高質(zhì)量、低成本、短交期的作業(yè)現(xiàn)場;
為企業(yè)規(guī)劃設計一套由內(nèi)到外的形象升級,外觀視覺價值體現(xiàn)、內(nèi)在的管理內(nèi)涵體現(xiàn);
全員參與設備管理高產(chǎn)出和低成本運營,提升設備管理能力,維護能力,提高效率
構建班組生產(chǎn)管理體系、循環(huán)評價、人才育成、持續(xù)改善、績效管理、文化養(yǎng)成體系;
提高產(chǎn)品質(zhì)量、降低生產(chǎn)成本、縮短交期、增加利潤,讓管理更系統(tǒng)科學,執(zhí)行力更強
對工廠的各個組成部分進行合理安排,以提高生產(chǎn)效率、降低成本、優(yōu)化物流、改善工作環(huán)境等