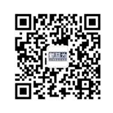
微信公眾號二維碼
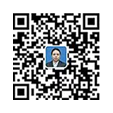
微信咨詢顧問二維碼
新益為TPM咨詢公司概述:精益生產是美國麻省理工學院國際汽車項目組的研究者給日本汽車工業(yè)的生產方式起的名稱。與傳統(tǒng)的大批量生產相比,精益生產只需要用一半的人員、 一半的生產場地、一半的投資、一半的生產周期、一半的產品開發(fā)時間和少得多的庫存,就能生產出品質更高、品種更多的產品。
精益生產
精益生產的實質是一種生產 管理技術,能夠大幅度減少閑置時間、作業(yè)切換時間、庫存、低劣品質、不合格的供貨商、產品開發(fā)設計周期及不及格的績效。它是繼大批量生產方式之后,對人類社會和人們的生活方式影響巨大的一種生產方式。
精益生產方式起源于日本豐田汽車公司。盡管精益生產的某些內容早在20世紀30年代就被日本企業(yè)所采用,但卻到了20世紀70年代豐田汽車公司的大野耐一通過應用精益生產方式把豐田汽車公司的交貨期和產品品質提高到世界領先地位時,精益生產才得到完全準確的描述。
精益生產的核心追求有以下兩個方面。
第一,追求零庫存。
精益生產是一種追求無庫存生產,或使庫存達到極小量的生產系統(tǒng),為此而開發(fā)了包括“看板”在內的一系列具體方法,并逐漸形成了一套獨具特色的生產經營體系。
第二,追求快速反應,即快速應對市場的變化。
為了快速應對市場的變化,精益生產者開發(fā)出了細胞生產、固定變動生產等布局及生產編程方法。
傳統(tǒng)的生產技術設定的目標是有限的。例如,在傳統(tǒng)的方式下,管理者們接受有少量缺陷的產品,也接受安全庫存量。而精益生產者則著眼于完美,目標是無不良品、無庫存,排除一切不產生價值的工作。通過提高產品品質、取消庫存、注重團隊合作和溝通、擴展員工的技術、培養(yǎng)員工的改善技能而不斷使他們自我提高,從而實現“0” 浪費的目標。在追求精益生產的過程中,精益生產者不斷地建立一個更好的生產體系,允許員工迎接更富有挑戰(zhàn)性的工作,允許他們更加迅速地對市場做出反應。
精益生產要求不斷取消那些不給產品增加價值的作業(yè)和工作。因此,我們可以認為精益生產的思想是一種持續(xù)減少浪費的哲學。
日本優(yōu)秀的企業(yè),特別是汽車制造業(yè),在20世紀六七十年代廣泛實施精益生產,獲得巨大成功,以低成本、高品質的產品享譽世界。到20世紀80年代,歐美國家、韓國及中國臺灣地區(qū)等制造業(yè)也開始引入精益生產。特別是美國制造業(yè),不僅僅引入,還基于自身發(fā)達的計算機技術,將精益生產的許多思想應用于ERP系統(tǒng)中,使其ERP系統(tǒng)在20世紀80年代開始領先世界。關于精益生產與ERP之間的關系,將在后面的章節(jié)中進行介紹。
精益生產的背景
日本汽車工業(yè)從第二次世界大戰(zhàn)以后開始起步,而此時從20世紀初就開始發(fā)展起來的美國汽車工業(yè)已達相當規(guī)模。例如,1950年,僅美國福特汽車公司的一個工廠日產量就達7000輛,而日本豐田汽車公司從其創(chuàng)立至1950年的十幾年間總產量僅為2650輛。
20世紀初,美國大眾的購買力增長很快,市場上汽車供不應求。福特汽車公司曾20年間連續(xù)生產型車,總產量為1500萬輛。依靠”單一品種大批量生產→以批量降低成本→成本的降低進一步帶來批量的擴大”這樣的方式造就了美國汽車工業(yè)的輝煌。
福特在T型車的生產過程中所創(chuàng)立的大批量生產方式奠定了現代汽車工業(yè)生產的基礎,揭開了現代化大生產的序幕。斯創(chuàng)立的“生產標準化原理”和“流水線組裝方式”在生產技術及生產管理史上也具有極為重要的意義。
不過,當世紀之輪轉到20世紀后半期,不僅美國,不僅是汽車工業(yè),許多發(fā)達國家整體上進入了消費者追求個性產品、相應市場需求開始向多樣化發(fā)展的新階段,因此要求工業(yè)生產也向多品種、小批量的方向邁進。
精益生產就是順應這樣的時代及市場要求,作為-種在多品種、小批量混合條件下高品質、低成本地進行生產的方式在實踐中被創(chuàng)造出來。20世紀50年代以來,尤其是70年代石油危機過后,采用精益生產方式的豐田汽車公司的經營績效與其他汽車制造企業(yè)的經營績效開始拉開距離,精益生產方式及其優(yōu)越性開始引起人們的注目和研究。
精益生產方式是豐田汽車公司在逐步擴大其生產規(guī)模的同時,為了實現滿足市場多樣化需求、快速應對市場變化的目標,經過20多年的努力發(fā)展起來的一門綜合管理技術。直到20世紀80年代,歐美國家、韓國及中國臺灣地區(qū)的大部分企業(yè)也全部或部分導入了精益生產方式。
建立生產有序、管理順暢,操作規(guī)范,士氣高昂、高質量、低成本、短交期的作業(yè)現場;
為企業(yè)規(guī)劃設計一套由內到外的形象升級,外觀視覺價值體現、內在的管理內涵體現;
全員參與設備管理高產出和低成本運營,提升設備管理能力,維護能力,提高效率
構建班組生產管理體系、循環(huán)評價、人才育成、持續(xù)改善、績效管理、文化養(yǎng)成體系;
提高產品質量、降低生產成本、縮短交期、增加利潤,讓管理更系統(tǒng)科學,執(zhí)行力更強
對工廠的各個組成部分進行合理安排,以提高生產效率、降低成本、優(yōu)化物流、改善工作環(huán)境等