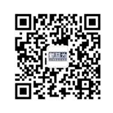
微信公眾號二維碼
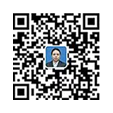
微信咨詢顧問二維碼
新益為精益生產(chǎn)咨詢公司概述:豐田模式就是日本管理的代名詞,其成功之處在于融會貫通。來自于福特,卻高于福特。在東方的文化土壤中,精益生產(chǎn)的出現(xiàn)絕對超乎了西方管理世界的想像。以至于,日本才是20世紀(jì)后半段全球管理的至高殿堂。
豐田精益生產(chǎn)
關(guān)于精益的書籍很多,經(jīng)典也很多,如果你想對這個話題有更深入了解的話,就從本文開始吧。還是那句話,文章很長,需要你耐心再耐心。但絕對值得!豐田模式就是日本管理的代名詞,其成功之處在于融會貫通。來自于福特,卻高于福特。在東方的文化土壤中,精益生產(chǎn)的出現(xiàn)絕對超乎了西方管理世界的想像。以至于,日本才是20世紀(jì)后半段全球管理的至高殿堂。
關(guān)于精益的書籍很多,經(jīng)典也很多,如果你想對這個話題有更深入了解的話,就從本文開始吧。還是那句話,文章很長,需要你耐心再耐心。但絕對值得!
精益生產(chǎn)(Lean Production,簡稱LP)是美國麻省理工學(xué)院數(shù)位國際汽車計劃組織(IMVP)的專家對日本“豐田生產(chǎn)方式”的贊譽之稱,精,即少而精,不投入多余的生產(chǎn)要素,只是在適當(dāng)?shù)臅r間生產(chǎn)必要數(shù)量的市場需要的產(chǎn)品;益,即所有經(jīng)營活動都要有益有效,具有經(jīng)濟性。精益生產(chǎn)是當(dāng)前工業(yè)界最佳的一種生產(chǎn)組織體系和方式。精益生產(chǎn)是戰(zhàn)后日本汽車工業(yè)遭到的“資源稀缺”和“多品種、少批量”的市場制約的產(chǎn)物,它從豐田相佐詰開始,經(jīng)豐田喜一郎及大野耐一等人的共同努力直到60年代才逐步完善而形成的。精益生產(chǎn)既是一種以最大限度地減少企業(yè)生產(chǎn)所占用的資源和降低企業(yè)管理和運營成本為主要目標(biāo)的生產(chǎn)方式,同時它又是一種理念,一種文化。實施精益生產(chǎn)就是決心追求完美的歷程,也是追求卓越的過程,也是一個永無止境的學(xué)習(xí)過程。
第一節(jié) “被迫”的精益生產(chǎn)
豐田的精益生產(chǎn),即豐田生產(chǎn)方式,是豐田在逐步學(xué)習(xí)之中,不斷改進而形成的,其形成的主要基礎(chǔ)來源于對于福特的學(xué)習(xí)以及豐田佐吉與豐田喜一郎在生產(chǎn)第一線總結(jié)的寶貴經(jīng)驗,可以說精益生產(chǎn)是在大規(guī)模生產(chǎn)的基礎(chǔ)上所提出的創(chuàng)新模式。然而,這種創(chuàng)新起初卻是“被迫”的創(chuàng)新,因為當(dāng)時以豐田的財力與規(guī)模根本不能發(fā)展大規(guī)模生產(chǎn),所以公司只能另辟新徑,嘗試小規(guī)模的精益生產(chǎn)。
一、學(xué)習(xí)福特
對于沒有技術(shù)、沒有經(jīng)驗的豐田來說,學(xué)習(xí)福特等國外先進企業(yè)是豐田必然的選擇。上世紀(jì)20年代,日本的汽車產(chǎn)量還不及美國一個月的汽車產(chǎn)量,豐田一年的總產(chǎn)量達不到福特一條生產(chǎn)線一天的產(chǎn)量,在當(dāng)時,美國汽車,以福特為首的大規(guī)模生產(chǎn)是世界學(xué)習(xí)的榜樣,大規(guī)模生產(chǎn)降低了生產(chǎn)成本,使得汽車開始了平民化的旅途。因此,剛剛成立的豐田也希望能夠?qū)W習(xí)福特的大規(guī)模生產(chǎn)以及其高超的生產(chǎn)技術(shù)。
1934年,豐田派技術(shù)兼作業(yè)部長菅隆俊訪問美國福特,考察美國汽車和零部件企業(yè),學(xué)習(xí)福特的汽車和零部件技術(shù)。菅隆俊訪問了130家工廠、7個研究所和5所大學(xué)。1938年,由菅隆俊設(shè)計指導(dǎo),豐田建立了第一座批量生產(chǎn)工廠——舉母工廠,這家工廠在布局上完全參照福特公司。舉母廠建立之后,豐田產(chǎn)量提升的同時,質(zhì)量問題突現(xiàn)出來,汽車的使用壽命一般只能維持一年,豐田曾經(jīng)試圖通過與福特公司創(chuàng)辦合資企業(yè)來學(xué)習(xí)其管理技術(shù)。然而,由于二戰(zhàn),合資學(xué)習(xí)的計劃擱淺,此后也沒有進行。
1950年的經(jīng)營危機,豐田接受銀行的融資之后,為了加快生產(chǎn),彌補技術(shù)的落后。1950年豐田高層再次掀起訪美熱潮。6~10月,神谷正太郎(豐田銷售公司總經(jīng)理)考察美國汽車產(chǎn)業(yè)的汽車消費金融問題。7~10月,豐田英二(豐田常務(wù)董事)抵達福特公司規(guī)模最大的底特律魯奇工廠考察,重點是其工程技術(shù)、生產(chǎn)管理、安全生產(chǎn)以及培訓(xùn)體制等。10~11月,齋藤尚一(豐田常務(wù)董事)隨日本通產(chǎn)省組織的日本汽車企業(yè)技術(shù)調(diào)查團訪美,齋藤也在福特魯奇工廠學(xué)習(xí)了一個半月,主要考察設(shè)備與工廠管理。
學(xué)習(xí)“福特”為豐田的生產(chǎn)奠定了重要的基礎(chǔ),“福特”成為豐田在汽車生產(chǎn)、研發(fā)和管理上的學(xué)習(xí)標(biāo)桿。
二、“被迫”的起因:大規(guī)模生產(chǎn)的不可能性
豐田的精益可以說是被迫的選擇,鑒于市場小、企業(yè)小、國家小等眾多原因,豐田不能選擇福特式的大規(guī)模生產(chǎn),需要另辟新徑,尋求適合其發(fā)展的生產(chǎn)方式。
1950年左右,豐田經(jīng)歷其傳奇歷程中最艱難的時刻,豐田汽車事業(yè)正處于萌芽時期,日本遭到兩顆原子彈的重創(chuàng),大多數(shù)產(chǎn)業(yè)都被摧毀,幾乎毫無供給,豐田本身資金嚴(yán)重短缺,此外,日本的消費者基本沒有什么錢,不具有大量購買汽車的能力。杰弗瑞·萊克在《豐田汽車案例-精益制造的14項管理原則》書中指出豐田不能實施“規(guī)模經(jīng)濟”的主要原因是規(guī)模經(jīng)濟與日本市場的矛盾;大量資金要求和豐田資金短缺的矛盾以及完整的供應(yīng)體系與豐田零部件供應(yīng)不足的。福特汽車公司的大規(guī)模生產(chǎn),其最核心的根本在于擴大規(guī)模、降低成本,只生產(chǎn)單一的車型,因此當(dāng)年福特的“T型車”只生產(chǎn)與供應(yīng)黑色的轎車??墒?,豐田面臨的情形非常不同,當(dāng)時的日本市場的任何一種車型的需求量都非常低,所以無法在同一生產(chǎn)線上大規(guī)模生產(chǎn),豐田必須使用相同的組裝線制造出不同車款。其次,福特汽車公司擁有充足的現(xiàn)金及龐大的美國與國際市場,而豐田既沒有現(xiàn)金,又生存于一個小國家,在缺乏資源與資本的情況下,豐田必須能快速周轉(zhuǎn)現(xiàn)金。最后,福特公司擁有完整的供應(yīng)體系,而豐田沒有完善的零部件供應(yīng)體系。鑒于這三個矛盾,豐田沒有本錢實施大規(guī)模生產(chǎn)方式。
面對種種矛盾,從美國考察回來的豐田二英與工廠經(jīng)理大野耐一進行了詳細討論與研究,決定改進大規(guī)模生產(chǎn)方式,使其適應(yīng)豐田與日本的情況。因此,豐田必須設(shè)法調(diào)整福特公司的制造流程,同時還必須實現(xiàn)高品質(zhì)、低成本及靈活彈性,正是在這種“不可能”的情形下,豐田開始了“精益生產(chǎn)”的道路。
三、豐田的改進
豐田決定改進大規(guī)模生產(chǎn),使其適應(yīng)日本與豐田的現(xiàn)狀。下表展示了豐田作出的改進。
此外豐田引進的質(zhì)量管理體系,是福特當(dāng)時所沒有的。全面質(zhì)量管理體系(TQC)是豐田生產(chǎn)方式的重要特征,豐田于1961年開始引進質(zhì)量,1963年,豐田全面推行了質(zhì)量管理體制,1965年獲得戴明質(zhì)量獎。
當(dāng)時,豐田作為一個不入流的汽車制造公司,學(xué)習(xí)福特是其必然的選擇,福特對于豐田來說,是一個標(biāo)桿企業(yè),然而,豐田并沒有完全照搬福特的生產(chǎn)以及流程,而是添加了其系統(tǒng)的思考與實地的調(diào)研,不斷改進大規(guī)模的生產(chǎn)方式,最終創(chuàng)造了一種有別于大規(guī)模生產(chǎn)、甚至改變世界的豐田生產(chǎn)方式。
第二節(jié) 貫穿運營各個環(huán)節(jié)的精益生產(chǎn)DNA
豐田基于“為顧客提供最方便和最有效的服務(wù)”的理念,經(jīng)過多年的改進和完善,終于建立了世界知名的豐田生產(chǎn)系統(tǒng)(Toyota Production System,縮寫為TPS),也就是精益生產(chǎn)系統(tǒng)。
兩大支柱:自働化和適時生產(chǎn)
豐田生產(chǎn)系統(tǒng)包含了兩個重要的理念:一是自働化(不嚴(yán)密的解釋為“帶有人情味的自動化”),其含義是,當(dāng)發(fā)生問題時,立即停止設(shè)備,防止有缺陷的產(chǎn)品產(chǎn)生;二是準(zhǔn)時生產(chǎn)(Just-in-Time),其含義是在流程中,每道工序只生產(chǎn)下道工序必須的產(chǎn)品?;谧詢P化和準(zhǔn)時生產(chǎn),TPS可以迅速地生產(chǎn)滿足顧客需求的汽車。
適時生產(chǎn)
“適時”意味著“在需要時,生產(chǎn)所必要的產(chǎn)品和必要的數(shù)額”。為了更加有效地生產(chǎn)大型的產(chǎn)品,例如由30000多個零部件組成的汽車,制定詳細地生產(chǎn)計劃是非常必要的。
按照生產(chǎn)計劃,“在需要時,生產(chǎn)所必要的產(chǎn)品和必要的數(shù)額”可以最大程度地消除浪費和不符合要求的產(chǎn)品,從而提高生產(chǎn)力。
“看板系統(tǒng)”是TPS中一個獨特的生產(chǎn)控制方法,看板系統(tǒng)對提高生產(chǎn)效率和質(zhì)量,發(fā)揮了重要作用??窗逑到y(tǒng)也被稱為“超市法”,因為看板系統(tǒng)背后的想法是來自超級市場。超市經(jīng)常使用商品控制卡,在控制卡上寫著產(chǎn)品的相關(guān)信息,如產(chǎn)品名稱,產(chǎn)品代碼以及存儲的位置。這些卡片可以使得員工迅速知道哪些產(chǎn)品的情況。在豐田,當(dāng)生產(chǎn)進入下一個流程的時候,操作人員使用看板溝通已經(jīng)使用了哪些零部件,還需要哪些零部件等等。
自動化
自動化在豐田生產(chǎn)系統(tǒng)中被定義為“帶有人情味的自動化”,自動化的理念可以追溯至豐田自動織機的創(chuàng)始人豐田佐吉,豐田佐吉發(fā)明的豐田自動織布機是日本第一太不需要人力的織布機。
1896年,豐田佐吉發(fā)明 “豐田織機”。隨后,他對自動織機做了了許多革命性的完善,其中最重要的是發(fā)明了緯線自動停止裝置,自動停止裝置的作用是一旦發(fā)現(xiàn)紡線斷了或者破損,自動停止裝置就立刻使得紡織機停止工作。在1924年,佐吉發(fā)明了世界上第一代的自動織機——“G型豐田自動織機”。
裝有自動停止裝置的紡織機發(fā)現(xiàn)問題的時候會自動停止工作,這樣一方面可以保障缺陷產(chǎn)品不會流向下一個流程,另一方面,可以停下來檢查問題,改進問題。自動停止使得問題可視化,使得人們對于問題一目了然,利于人們解決問題和不斷改進。
安燈系統(tǒng)
安燈系統(tǒng)(ANDON)是一種現(xiàn)代企業(yè)的信息管理工具。Andon也稱暗燈或安燈,原為日語的音譯,日語的意思為“燈”、“燈籠”,在這里表示一個系統(tǒng), Andon系統(tǒng)能夠收集生產(chǎn)線上關(guān)于設(shè)備和質(zhì)量等信息,加以處理后,通過控制分布于車間各處的燈光和聲音報警系統(tǒng),使得問題可視化,從而實現(xiàn)生產(chǎn)信息的透明化。
豐田生產(chǎn)方式的安燈系統(tǒng)風(fēng)靡制造業(yè)。目前,在汽車制造的各大車間都可以看到針對不同需求而設(shè)計的安燈。而且它應(yīng)用在各個門類的機械制造廠中,發(fā)揮著警示作用和及時的信息傳遞作用,安燈系統(tǒng)將問題阻止在最初的地方并及時解決問題的作用,它是一種提高生產(chǎn)質(zhì)量和效率的最有效的手段。
一個思想:杜絕一切浪費
豐田精益生產(chǎn)最大的敵人就是浪費,豐田生產(chǎn)方式的鼻祖大野耐一說道“徹底杜絕一切浪費”。企業(yè)只有通過增加利潤才可以獲得生存的權(quán)利。計算利潤的傳統(tǒng)方式是“銷售價=利潤+原價”,然而豐田得方式是“利潤=銷售價-原價”。兩個公式或許在數(shù)學(xué)上是一致的,但是有著本質(zhì)的區(qū)別,傳統(tǒng)的公式意味著提高銷售價才能獲得利潤,而豐田的公式意味著降低成本才能獲得利潤。豐田認(rèn)為杜絕一切可能的浪費是獲得利潤的根本方式,生產(chǎn)流程過程和企業(yè)管理中不能為顧客創(chuàng)造價值的環(huán)節(jié)都是浪費,都會導(dǎo)致成本的增加。
生產(chǎn)過剩和缺陷產(chǎn)品,是豐田認(rèn)為的最大浪費。生產(chǎn)過量必然會導(dǎo)致下一個流程的存貨增加,而存貨的增加則需要相應(yīng)的人去管理、多余的地方去存放它,企業(yè)還要為了防止存貨丟失和損壞,投入巨大的資金;缺陷產(chǎn)品也是企業(yè)的大敵,銷毀缺陷品不僅僅是損壞了這件產(chǎn)品的價值,而是浪費了企業(yè)生產(chǎn)、保存和運輸這件產(chǎn)品的投入和人力。
八種浪費的形式
1.生產(chǎn)過剩:生產(chǎn)出尚未有訂單的產(chǎn)品,造成人員過多和過多存貨,從而導(dǎo)致儲存與輸送等成本的浪費。
2.在現(xiàn)場等候的時間:員工只是在一旁監(jiān)看自動化機器,或必須站在一旁等候下一個處理步驟、工具、供應(yīng)、零部件等,或是因為存貨用完、整批處理延遲、機器設(shè)備停工、產(chǎn)能瓶頸等因為造成員工暫時沒有工作可做。
3.不必要的運輸:長距離搬運在制品,缺乏效率的運輸,進出倉庫或在流程之間搬運原材料、零部件或最終成品。
4.過度處理或不正確的處理:采取不必要的步驟以處理零部件;因為工具與產(chǎn)品設(shè)計不良,導(dǎo)致不必要的動作及產(chǎn)生瑕疵而造成缺乏效率的處理;當(dāng)提供超出必要的較高品質(zhì)產(chǎn)品時,也會造成浪費。
5.存貨過剩:過多原料、在制品或最終成品,導(dǎo)致較長的前置期、陳舊過時品、毀損品、運輸與儲存成本及延遲。此外,過多存貨還造成其他隱藏性問題,例如生產(chǎn)不均衡、供應(yīng)者延遲遞送、瑕疵品、機器設(shè)備停工、拉長整備期(setup time)。
6.不必要的移動搬運:員工在工作的過程中,任何浪費、不必要的動作,例如尋找、前往拿取,或是堆放零部件、工具等。此外,走動也是浪費。
7.瑕疵:生產(chǎn)出瑕疵品或必須返工的東西。修理或重做、報廢、更換生產(chǎn)、檢驗等,意味著處理、時間與精力的浪費。
8.未被使用的員工創(chuàng)造力:由于未使員工參與、投入或未能傾聽員工意見而造成未能善用員工的時間、構(gòu)想、技能,使員工失去改善與學(xué)習(xí)機會。
杜絕一切浪費是豐田精益管理的一個核心思想,也是其取得成功的關(guān)鍵,豐田各種管理制度和體制為了消除以上八種浪費而制定。
實施途徑: 全面質(zhì)量管理
全面質(zhì)量管理是豐田實施精益管理的兩種重要途徑。豐田通過全面質(zhì)量管理獲得了優(yōu)質(zhì)的質(zhì)量,促使豐田打敗美國企業(yè),后來者居上。
全面質(zhì)量管理的概念
豐田的全面質(zhì)量管理包含兩層意思:第一是指產(chǎn)品生產(chǎn)“全過程”的質(zhì)量管理,第二是指有全體員工參加的“全員管理”。“全員管理”是豐田等日本企業(yè)在實踐質(zhì)量管理的過程中,對歐美質(zhì)量管理的改進,豐田等日本企業(yè)注重發(fā)揮人的作用,這是日本推行全面質(zhì)量管理的最大特點,也是豐田質(zhì)量管理的最大特點。
所謂“全過程”是指①產(chǎn)品規(guī)劃;②產(chǎn)品設(shè)計;⑤試制、試驗;④生產(chǎn)準(zhǔn)備(包括工序配備、檢查計劃、工序管理計劃等);⑥批量投產(chǎn);⑥產(chǎn)品制造質(zhì)量檢查(包括工藝檢查及出廠檢查試驗等),⑦銷售服務(wù)(包括包裝、運輸、保修、索賠等)這七個階段。每個階段都有嚴(yán)格的質(zhì)量要求和檢查規(guī)定,最后的目的就是為用戶提供高質(zhì)量的產(chǎn)品。
所謂全員管理,就是指在整個質(zhì)量管理推行的過程中,充分發(fā)揮全體員工的積極性與能動性。“全員”不僅僅指企業(yè)的全體人員,而且包括整個公司,整個系統(tǒng)及其所屬的一切部門。歐美企業(yè)的質(zhì)量管理主要是依靠專家的作用。而豐田的質(zhì)量管理涉及到各個部門,從生產(chǎn)到售后服去,涉及到各個階層經(jīng)理、中層干部、專家以及普通員工。這種全員參加,使得質(zhì)量管理覆蓋到企業(yè)的每一個角落,任何部門、任何個人都需要注重提高自己工作的質(zhì)量、提高產(chǎn)品的質(zhì)量。充分發(fā)揮每一位員工的作用,是豐田全面質(zhì)量管理的成功之處。
豐田全面質(zhì)量管理的特點:
綜合山本直的《豐田四十年的歷程》以及《日本豐田汽車企業(yè)集團及其經(jīng)營管理》中對豐田全面質(zhì)量管理的描述,總結(jié)豐田全面質(zhì)量管理具有如下特點:
一是質(zhì)量小組——全員參與的基礎(chǔ)
豐田全面質(zhì)量管理之所以可以實現(xiàn)全員管理,最重要的原因在于質(zhì)量小組的組建。質(zhì)量小組使得每一位員工都有機會發(fā)表意見和提出解決方案。
日本的質(zhì)量小組最初是由車間工人自發(fā)組織起來的,主要是學(xué)習(xí)質(zhì)量管理知識,并結(jié)合車間的問題,共同研討質(zhì)量改進的措施。1964年,豐田開始了質(zhì)量小組活動。小組按車間組建,每組10人左右。各小組自行選擇本車間問題,進行研究和改進。組織和選題都可向公司登記。一個課題完成后,再自動選擇下一個課題。這種活動方式,豐田稱為“滾動方式”。公司對質(zhì)量管理部對質(zhì)量小組具有引導(dǎo)、服務(wù)、援助的義務(wù),并為質(zhì)量小組提供各種信息和輔導(dǎo),也可以根據(jù)公司發(fā)展的需求提出共同性課題來推動小組活動。質(zhì)量小組活動是自愿的,并無報酬。但每半年要舉行一次“小組活動事例發(fā)表會”,對優(yōu)秀的小組予以表揚,對提出合理化建議的給予獎勵。質(zhì)量管理小組的活動,對激發(fā)員工的潛能、對改進質(zhì)量和降低成本,都取得很大的成果。
二是注重培訓(xùn)
為了使整個質(zhì)量活動能更好地進行,豐田重視對員工的培訓(xùn),所有的員工上崗前要進行380小時的質(zhì)量培訓(xùn)。進入豐田的大學(xué)生要用三個月的時間學(xué)習(xí)質(zhì)量管理課程,提高解決實際質(zhì)量問題的能力和制定解決質(zhì)量問題方案的能力。豐田對員工質(zhì)量的培訓(xùn)時間比歐洲廠家多出1倍,在實際工作中豐田員工的差錯率要比歐洲廠家少得多。大力培訓(xùn)促使豐田質(zhì)量理念深入人心,保障了全面質(zhì)量管理的順利進行。
三是質(zhì)量、成本和安全的平衡
提高質(zhì)量雖然重要,但是不能不顧成本地一味追求質(zhì)量越高越好。因為過高的質(zhì)量很可能超出消費者的需求,成為多余的質(zhì)量,而且過高的質(zhì)量會導(dǎo)致成本的提高,這也不利于滿足消費者的物美價廉需求。此外,機械操作的安全性和設(shè)備的維修保養(yǎng)既影響質(zhì)量,也影響成本。因此,豐田的質(zhì)量管理注重三者之間的平衡,提高產(chǎn)品的質(zhì)量、降低產(chǎn)品的成本,打造產(chǎn)品的競爭力。
合理化建議——持續(xù)改善的基礎(chǔ)
豐田生產(chǎn)方式中最重要的持續(xù)改善來源于豐田幾千名員工的建議,每人一條好的建議,企業(yè)怎么能夠不吃細改善。
“好主意、好產(chǎn)品”是豐田合理化建議的核心。合理化建議是豐田學(xué)習(xí)福特“建議制度”的結(jié)果,然而卻成為90年代美國學(xué)習(xí)豐田的榜樣。這樣的轉(zhuǎn)變原因在于豐田對建議制度的合理化改進。1951年,到福特汽車參觀學(xué)習(xí)的豐田英二和齋蘸尚一(曾任豐田的董事長),發(fā)現(xiàn)福特汽車的“建議制度”對激發(fā)員工出謀劃策,改善企業(yè)的產(chǎn)品,非常有效和省錢。50年代,豐田剛剛走出破產(chǎn)的陰霾,非常缺乏資金。因此,豐田英二等認(rèn)為建議制度可以激發(fā)員工潛能,幫助企業(yè)用最少的錢做最多的事情?;貒?,立刻開始著手建立豐田的“建議制度”,即合理化建議活動。
20世紀(jì)50年代,合理化的建議范圍主要集中于機械、技術(shù)。70年代后,范圍逐漸擴展至成本和質(zhì)量方面。合理化建議經(jīng)過多年的發(fā)展,已經(jīng)覆蓋所有的流程和業(yè)務(wù),涉及生產(chǎn)、研發(fā)、營銷以及經(jīng)營管理的各個方面。豐田的合理化建議發(fā)揮了激發(fā)員工參與和調(diào)動員工積極性的作用。集思廣益的意見可使得豐田不斷改進、不斷創(chuàng)新、不斷挑戰(zhàn)新的高峰。
豐田的合理化建議之所以能夠真正地發(fā)揮作用,而不是像其它企業(yè)那樣形同虛設(shè),最重要的原因有以下幾點:
第一是認(rèn)可和采納員工的意見。認(rèn)可和采納意見是對員工最大的尊重和鼓勵,這不僅是對員工參與的最高獎勵,而且實施員工所提出的意見必將贏得員工的支持,執(zhí)行過程中,員工會投入最大熱情和努力。1976年所采納的意見數(shù)達到五十八萬六千二百七十五件,采納率達到83%,每個員工平均被采納的意義達到8.8件。
第二是高物資回報。對于員工提出的優(yōu)秀建議,豐田會給予相當(dāng)豐厚的物資回報。豐田按七個項目評分對建議成果進行審查,分別是有形效果;無形效果;利用程度;獨創(chuàng)性;設(shè)想的性質(zhì);職務(wù)減分(如建議如果屬于員本身職務(wù)的專業(yè)應(yīng)予減分)。每頂均按5—20分的級別評分,總分100為滿分。質(zhì)量特別優(yōu)秀的分?jǐn)?shù)不作上限。獎金的級別最低為500日元,最高為20萬日元,特別優(yōu)秀的也不作上限。
第三是高層、技術(shù)和普通員工的參與。參加活動的人員,有高層領(lǐng)導(dǎo),有專業(yè)的技術(shù)骨干,再加上一般員工。通過共同商討,分級評審以及展覽講評等靈活多樣的形式,把全體員工都納入公司預(yù)定的活動軌道,最大程度調(diào)動員工的參與性和積極性。
第四是企業(yè)給予大方面的指導(dǎo)。員工的建議不能完全是脫離公司情況,這些意見必須是能夠解決公司問題的。因此,豐田隨時向員工和各個部門發(fā)布公司的理想和思路,為參加活動的廣大員工提供信息,指明方面。例如,目前,豐田所提供的特別方面,就是環(huán)保技術(shù)、節(jié)約能源等。這些指導(dǎo)幫助員工做出最佳的意見,也是幫助企業(yè)取得最大的成功。
豐田的合理化建議制度,以及成本管理和質(zhì)量管理這一套學(xué)問,本來都是從美國汽車制造業(yè)的三大巨頭,特別是從福特公司那里學(xué)來的。但他在實際運用上既不拘泥于老師規(guī)定的教條,也不是把三者分開采孤立地分頭員徹,而是針對自己的實際情況,結(jié)果青出于藍而勝于藍,收效遠遠超過美國。不但超越,美國又反過來學(xué)習(xí)豐田,由此可見豐田的學(xué)習(xí)和改善能力。
第三節(jié) 不經(jīng)世代,無以致精益
精益生產(chǎn)來源于豐田生產(chǎn)方式,豐田生產(chǎn)方式是豐田歷代人的心血積累,每一代的豐田人都致力于消除浪費,提高效率,豐田佐吉與豐田喜一郎奠定了豐田的哲學(xué)基礎(chǔ)——“自動化”與“適時生產(chǎn)”,大野耐一與豐田英二將理念轉(zhuǎn)化為真正的生產(chǎn)力,最終創(chuàng)造了聞名世界的豐田生產(chǎn)方式。
一、豐田哲學(xué)的奠基
徹底消除浪費與追求最有效的生產(chǎn)方法是豐田生產(chǎn)系統(tǒng)的宗旨,這可以追溯至豐田佐吉的紡織時代。通過多年的試錯與改進,在豐田佐吉思想的基礎(chǔ)上不斷改進形成豐田生產(chǎn)方式。豐田佐吉發(fā)明的自動織機不僅僅可以不依靠人力而自動的工作,而且能夠?qū)C器本身做出判斷,一旦發(fā)現(xiàn)殘次品就立即停止。而正是這種“一旦發(fā)生次品,機器立即停止運轉(zhuǎn),以確保百分之百的品質(zhì)”的思考方式,奠定了豐田的精益生產(chǎn)的思想基礎(chǔ)——不斷改進、消除缺陷、保障質(zhì)量等等。豐田喜一郎,繼承了這一思想,并且在此基礎(chǔ)上,開創(chuàng)了“準(zhǔn)時生產(chǎn)”的理念和生產(chǎn)方式。
豐田佐吉——自動化的思想
豐田一貫強調(diào)的自動化是“帶人字旁的自動化”。“有人字旁的自動化”的精神,源于豐田“鼻祖”豐田佐吉所發(fā)明的自動織機。“有人字旁的自動機器”在豐田是指“具有自動停止裝置的機器”。在豐田,幾乎工廠里的每一套機器設(shè)備都裝備了自動停止裝置。機器在正常運轉(zhuǎn)時根本不需要人,只在發(fā)生異常情況才需要人。豐田的自動化有兩重含義:一是機器自身的自動化作業(yè);二是操作者負責(zé)監(jiān)督機器,出現(xiàn)問題要馬上解決,不允許產(chǎn)生劣質(zhì)產(chǎn)品。
“自動化”生產(chǎn)思想包含兩個關(guān)鍵,即生產(chǎn)信息傳遞的自動化以及生產(chǎn)的流動化。生產(chǎn)過程實際就是生產(chǎn)信息的傳遞過程,如何使生產(chǎn)信息在生產(chǎn)中準(zhǔn)確無誤地傳遞,成為豐田所追求的最高目標(biāo)。自動化思想目的是消除生產(chǎn)信息傳遞過程中的信息錯誤或遺漏現(xiàn)象,其運營原則就是當(dāng)作業(yè)過程中發(fā)生任何異常時,機器或生產(chǎn)線自身就能夠立即做出判斷而停止運轉(zhuǎn),從而發(fā)現(xiàn)和消除作業(yè)中存在的隱患。
豐田喜一郎——準(zhǔn)時生產(chǎn)
準(zhǔn)時生產(chǎn)就是“將必要的產(chǎn)品,在必要的時間,提供必要的數(shù)量”,用準(zhǔn)時化來最大限度地避免生產(chǎn)浪費現(xiàn)象。準(zhǔn)時化生產(chǎn)是由豐田喜一郎對生產(chǎn)實踐中經(jīng)驗的總結(jié)與升華。
1938年豐田喜一郎提出了“準(zhǔn)時生產(chǎn)”思想的建廠原則,“大小三十幾個分廠,要形成有利于生產(chǎn)的合理布局”,“工廠內(nèi)的各種專業(yè)設(shè)備,要像細胞組織一樣形成緊密關(guān)聯(lián)”,他還特別強調(diào)“要摒棄建廠就必須建倉庫的傳統(tǒng)”,提出了“零庫存”概念。
上世紀(jì)30年代,在接受《內(nèi)燃機》雜志專訪時,豐田喜一郎全面闡述了準(zhǔn)時生產(chǎn)思想.“在汽車工業(yè)中,無論是從質(zhì)還是從量上講,材料都具有非常重要的作用。汽車生產(chǎn)僅零部件種類就有兩三千種之多,若不好好考慮原材料及零部件的準(zhǔn)備和庫存,勢必會耗費大量資金。我認(rèn)為應(yīng)避免‘過猶不及’,也就是說,對于指定生產(chǎn)不要投人過份勞力和時間,避免出現(xiàn)浪費和過?,F(xiàn)象。通過零部件的移動和循環(huán)來避免‘窩工’現(xiàn)象,‘恰好準(zhǔn)時’地準(zhǔn)備好各種部件,這也是效率第一主義,甲零件準(zhǔn)備過多、過早,勢必會使乙零件過少、過慢。小到一個螺釘或螺母,所有零部件都要正好準(zhǔn)時”。
準(zhǔn)時化的生產(chǎn)讓“庫存”接近于最低程度,這就衍生出豐田生產(chǎn)方式的另一特征——零庫存。要在生產(chǎn)實踐中真正實現(xiàn)準(zhǔn)時生產(chǎn)非常困難,為此,豐田創(chuàng)造了一系列輔助體制,如“看板管理”方式、“倒流水”生產(chǎn)流程等,這些體制都為實現(xiàn)準(zhǔn)時生產(chǎn)創(chuàng)造了前提條件。
二、理念成為現(xiàn)實
豐田佐吉與豐田喜一郎的思想是豐田生產(chǎn)系統(tǒng)以及豐田經(jīng)營的基礎(chǔ)與根本,然而這些思想當(dāng)時在豐田并沒有真正地落實,豐田英二與大野耐一才真正地將豐田的哲學(xué)轉(zhuǎn)化為生產(chǎn)力,創(chuàng)建了系統(tǒng)化的豐田生產(chǎn)方式,并將這種生產(chǎn)方式運用于整個工廠與供應(yīng)商,使得豐田成為世界上效率最高、成本最低的企業(yè)。
(一)拉動式生產(chǎn)的推進
拉式制度是大野耐一從美國超級市場的操作流程中學(xué)到的一種生產(chǎn)方式。大野耐一在美國訪問的時候發(fā)現(xiàn),在運營表現(xiàn)優(yōu)良的超級市場,當(dāng)貨架上陳列的個別商品數(shù)量減至相當(dāng)少時,才會進行補貨作業(yè),也就是說,材料的補充根據(jù)消費情形而定。如果把這個原則應(yīng)用到工廠生產(chǎn),即第一步應(yīng)該等到下一步(第二步)用完或接近用完第一步所供應(yīng)的材料或零部件時(亦即已經(jīng)接近最低安全存量時),才進行補貨作業(yè)。于是大野耐一創(chuàng)立了豐田生產(chǎn)方式中最重要的理念——拉動式生產(chǎn),而其實施的基礎(chǔ)就是“看板”體系。
杰弗瑞·萊克在《豐田汽車案例-精益制造的14項管理原則》中解釋拉動式生產(chǎn)的過程是:拉動式生產(chǎn)中,由后面的流程拉動前面的生產(chǎn)流程,一個拉動一個,直至生產(chǎn)流程的第一步;拉動式生產(chǎn)是一種“逆向”去控制生產(chǎn)數(shù)量的供應(yīng)鏈模式,這種方式不僅能節(jié)省庫存成本(達到零庫存),更重要的是能夠提高流程效率;當(dāng)流程的第二步的材料或零部件已經(jīng)降低至最低安全存量時,就會發(fā)出信息,通知流程的第一步供應(yīng)更多材料或零部件,而信息的傳遞則依賴于“看板”。“看板”是豐田生產(chǎn)方式的關(guān)鍵,是實現(xiàn)“準(zhǔn)時化”的管理工具。所謂“看板”,是指記載著后一道工序向前一道工序取用物品等相關(guān)信息的卡片,一般是用小紙片放入方形塑料膠袋中.上面記載著要取用“什么、多少”以及“要生產(chǎn)什么、生產(chǎn)方法”等,雖然看板僅僅是記載了所需的物品,然而就是這個小小的改變重新改造了流程,改變了傳統(tǒng)前端的操作者主導(dǎo)生產(chǎn)數(shù)量,而變成重視后端顧客需求,后面的作業(yè)人員通過看板告訴前一項作業(yè)人員需求,比如零件需要多少,何時補貨。
有了科學(xué)理念之后,就是一步一步地實踐。1948年,豐田開始推行拉動式生產(chǎn),大野耐一對此解釋說,“生產(chǎn)流程無非就是物品流動,我是逆向思考這種物品搬運過程的:以往一般是‘前工序?qū)⑽锲匪徒o后工序’……但我想,如果‘后工序在必要的時候,向前工序領(lǐng)取必要數(shù)量該物品的話’,那么‘前工序不就可以只生產(chǎn)被領(lǐng)走的數(shù)量’了嗎”?1953年,大野率先在機械車間引進了“看板方式”,接著將之從組裝線、車體車間等依次向前工序推進,1959年新建投產(chǎn)的元町工廠全部采納拉動式生產(chǎn),1962年,大野耐一將該方式推及全部生產(chǎn)工序,至此,豐田生產(chǎn)工廠內(nèi)基本建立了拉動式生產(chǎn)方式。
(二)多功能工
多功能工,是指一個操作工人可以操作不同的機械。如果一個人可以管理兩臺機器,那么企業(yè)的效率便會得到大大提升, “多能工”一方面可以以降低企業(yè)的成本,一方面可以提高生產(chǎn)的靈活性。多功能工促使豐田實現(xiàn)低成本和彈性的生產(chǎn)。“多能工”體制以及“少人化”成為豐田的生產(chǎn)目標(biāo)。
(三)可視化管理
可視化管理是豐田生產(chǎn)方式的重要組成部分,所謂“可視”是指管理者或監(jiān)督者對生產(chǎn)過程一目了然,一下子就知道操作人員是否按照標(biāo)準(zhǔn)作業(yè)在進行操作。在豐田生產(chǎn)方式中,可視化管理是與標(biāo)準(zhǔn)化作業(yè)緊密關(guān)聯(lián)的一項制度,它是實現(xiàn)“自動化”生產(chǎn)目標(biāo)的重要措施。自動化就是說生產(chǎn)中發(fā)生異常,便能立刻停止機器或生產(chǎn)線,其基本要求是必須弄清楚什么是正常、什么是異常。1950年,豐田首先在發(fā)動機組裝線實施了“燈籠方式”的可視化管理,生產(chǎn)正常運轉(zhuǎn)時顯示綠燈;而操作人員需要幫助時,可亮起黃燈;若出現(xiàn)問題而需要徹底停止生產(chǎn)線檢查時,亮起紅燈。
(四)持續(xù)改進
豐田在其“每日改善”的哲學(xué)中汲取美國質(zhì)量管理大師愛德華·戴明(W. Edward Deming)所傳授的東西。戴明鼓勵日本采取有系統(tǒng)的方法解決問題,此即后來所謂的“戴明循環(huán)”(Deming Cycle),或“規(guī)劃——執(zhí)行——檢查——行動”(Plan-Do-Check-Act, PDCA),這是進行持續(xù)改進的基石。持續(xù)改進的日語是kaizen,是漸進、遞增式的改進(不論改進有多么小),以去除并杜絕只增加成本、卻未能創(chuàng)造價值的所有浪費。持續(xù)改進是豐田生產(chǎn)方式得以完善與發(fā)展的基礎(chǔ),并在日常運作中維系豐田生產(chǎn)方式的重要原則。
(五)廣泛推廣豐田生產(chǎn)方式
零部件企業(yè)在汽車產(chǎn)業(yè)鏈中發(fā)揮重要的作用,因此將豐田生產(chǎn)方式推廣到上游的零部件企業(yè)是豐田提升汽車質(zhì)量的重要手段。1936年,日本為了保護國內(nèi)汽車產(chǎn)業(yè),頒布了《汽車生產(chǎn)事業(yè)法》,根據(jù)這條法例,國內(nèi)企業(yè)不能進口國外的特殊鋼鐵以及一些重要零部件。在保護國內(nèi)汽車產(chǎn)業(yè)的同時,使得豐田等汽車企業(yè)必須使用國內(nèi)質(zhì)量低下的產(chǎn)品,直接影響豐田的效率與質(zhì)量,因此提高上游零部件企業(yè)的產(chǎn)品質(zhì)量和生產(chǎn)效率勢在必行。
1960年,大野耐一把他的思想推廣到豐田內(nèi)部的全部生產(chǎn)工廠,對豐田的所有供應(yīng)商開始實行準(zhǔn)時化供貨;1965年將看板方式推廣至零部件供應(yīng)企業(yè),通過實施技術(shù)指導(dǎo),促進并實現(xiàn)了零部件供應(yīng)商與豐田的生產(chǎn)同步化。然而,豐田發(fā)現(xiàn)供應(yīng)商只是看上去是精益生產(chǎn)。他們快速小批量的發(fā)貨來源于其成品庫中提前準(zhǔn)備好的一小堆一小堆的零件,這些零件仍然源自大規(guī)模的生產(chǎn),而不是按照豐田生產(chǎn)方式生產(chǎn)的。豐田的供應(yīng)商仍然不知道如何利用豐田生產(chǎn)方式,進行小批量的生產(chǎn)滿足豐田的需求。因此,1969年,大野耐一建立生產(chǎn)研究辦公室(經(jīng)營管理咨詢部OMCD),目的是要在豐田的42家最大的和最重要的供應(yīng)商中建立互助小組,幫助他們徹底學(xué)會豐田生產(chǎn)方式。這些公司被分成六個小組,每組由七家組成,并由其中一家公司出任小組負責(zé)人。要求這些小組每月都要在經(jīng)營管理咨詢部的技術(shù)支持下,在小組成員企業(yè)中,進行一次重大的改進活動。每一家企業(yè)改進活動的結(jié)果都要有另外六家公司的高級管理人員進行檢驗,他們的任務(wù)是要就如何進行進一步改進的問題出建議。然后,又要求這些供應(yīng)商建立他們自己的經(jīng)營管理咨詢部,開始進行使每一項活動都精益化的工作。在豐田不斷要求降低成本的情況下,第一層供應(yīng)商認(rèn)識到有必要通過在第二層供應(yīng)商中傳授豐田生產(chǎn)系統(tǒng),來降低第二層供應(yīng)商成本。按照這種方式,1970年末,豐田生產(chǎn)方式沿著供貨鏈得到廣泛傳播。
三、世界知名的精益生產(chǎn)
大野耐一和他的團隊建立的新的豐田生產(chǎn)方式,并非只針對特定市場與文化的某個公司。他們所發(fā)展出來的是一個適用于制造業(yè)或服務(wù)業(yè)的新模式,它以全新方式看待、了解與詮釋生產(chǎn)流程,它優(yōu)于大規(guī)模生產(chǎn)方式。
到了20世紀(jì)60年代,豐田生產(chǎn)方式已經(jīng)成為所有類型的企業(yè)可以學(xué)習(xí)應(yīng)用的理念。豐田首先通過把豐田生產(chǎn)方式的原則傳授給它的主要供貨商來倡導(dǎo)精益的概念及做法。此舉使豐田從單獨實施精益的制造工廠邁向全面實施精益的企業(yè)——價值鏈上的每個廠商都采用相同的豐田生產(chǎn)方式,這實在是一個強力的企業(yè)模式!
不過,當(dāng)時,在豐田及其供貨商之外,豐田生產(chǎn)方式的效能幾乎不為人知。直到1973年第一次石油危機造成全球經(jīng)濟蕭條,日本尤其受到了最嚴(yán)重打擊,日本產(chǎn)業(yè)陷入混亂,所有企業(yè)都掙扎著謀求生存,日本政府注意到豐田汽車公司發(fā)生虧損的時間比其他企業(yè)短,并且能快速恢復(fù)生產(chǎn)力。于是,日本政府主動舉辦豐田生產(chǎn)方式研討會,但是它只了解豐田生產(chǎn)方式的部分訣竅而已。
1985年,為了進一步揭開日本汽車工業(yè)成功之謎,美國麻省理工學(xué)院籌資500萬美元,確定了一個名叫“國際汽車計劃”(IMVP)的研究項目。在丹尼爾·魯斯教授的領(lǐng)導(dǎo)下,組織了53名專家、學(xué)者.從1984年到1989年,用了五年時間對14個國家的近90個汽車裝配廠進行實地考察。最后于1990年著出了《改變世界的機器》一書,第一次把豐田生產(chǎn)方式定名為 Lean Production,即精益生產(chǎn)方式。這個研究成果引起了汽車業(yè)內(nèi)的轟動,掀起了一股學(xué)習(xí)精益生產(chǎn)方式的狂潮。精益生產(chǎn)方式的提出,把豐田生產(chǎn)方式從生產(chǎn)制造領(lǐng)域擴展到產(chǎn)品開發(fā)、協(xié)作配套、銷售服務(wù)、財務(wù)管理等各個領(lǐng)域,貫穿于企業(yè)生產(chǎn)經(jīng)營活動的全過程,使其內(nèi)涵更加全面,更加豐富,對指導(dǎo)生產(chǎn)方式的變革更具有針對性和可操作性。
接著在1996年,經(jīng)過四年的“國際汽車計劃”(IMVP)第二階段研究,著出了《精益思想》這本書?!毒嫠枷搿窂浹a了前一研究成果并沒有對怎樣能學(xué)習(xí)精益生產(chǎn)的方法提供多少指導(dǎo)的問題,而這本書則描述了學(xué)習(xí)豐田方法所必須的關(guān)鍵原則,并且通過例子講述了各行各業(yè)均可遵從的行動步驟,進一步完善了精益生產(chǎn)的理論體系。
在此階段,美國企業(yè)界和學(xué)術(shù)界對精益生產(chǎn)方式進行了廣泛的學(xué)習(xí)和研究,提出很多觀點,對原有的豐田生產(chǎn)方式進行了大量的補充,主要是增加了很多IE技術(shù),信息技術(shù),文化差異等對精益生產(chǎn)理論進行完善,以使精益生產(chǎn)更適用性。
第四節(jié) 精益思想的精髓
很多企業(yè)都在學(xué)習(xí)豐田,然而基本沒有企業(yè)可以達到像豐田一樣的精益,這是因為,他們學(xué)習(xí)的僅僅是豐田生產(chǎn)方式的形式,如看板、多功能工等等,而沒有看到這種精益背后的原則與思想。這些原則和思想是豐田在70多年的發(fā)展中逐漸形成的,甚至身在其中的豐田自己可能都沒有意識到他們的存在。但是,正是這些融入豐田的原則和思想是豐田實現(xiàn)精益的關(guān)鍵。下面兩篇論文的作者經(jīng)過在豐田多年的調(diào)查和研究,將這些隱藏的原則與思想公之于眾。
一、豐田精益生產(chǎn)的DNA
豐田精益體系中一個明顯的悖論——豐田工廠中的各種活動、工作銜接和生產(chǎn)流程都有嚴(yán)格的明文規(guī)定,但實際操作卻非常靈活、有很強的適應(yīng)性。而且,這些活動和流程常常在人們的挑戰(zhàn)和質(zhì)疑之中被推向更高一層的績效水平,使得豐田能夠持續(xù)創(chuàng)新和改進。
豐田生產(chǎn)體系以及在背后支撐該體系的科學(xué)方法,并不是強制推行的,甚至也不是有意為之,而是經(jīng)過50多年,慢慢地于實踐中自然而然形成的。Steven spear和 H.Kent Bowen經(jīng)過多年研究,在《Decoding the DNA of the Toyota Production System》詳述了豐田生產(chǎn)方式背后的四條原則,其中三條是設(shè)計規(guī)則,說明豐田如何將所有的作業(yè)流程變成一項項實驗;另一條是改進規(guī)則,講述豐田怎樣把科學(xué)方法傳授給組織中各個層級的工人。正是這些原則,而非人們在參觀工廠時所看到的具體做法和實用工具,成了豐田生產(chǎn)方式的精髓。這些原則是豐田生產(chǎn)體系的DNA。
規(guī)則一:必須對每項作業(yè)活動詳加說明
細節(jié)決定成敗,所以要確保所有作業(yè)的內(nèi)容、次序、時間安排和最終結(jié)果都有明確規(guī)定。例如,在安裝汽車座椅的時候,工人們總是依照一定的次序來上螺栓,而擰緊每個螺栓所需的時間和轉(zhuǎn)矩也都有明確規(guī)定。這種精確性不僅體現(xiàn)在生產(chǎn)工人的重復(fù)性動作中,也反映在所有員工的作業(yè)中,無論他們屬于哪個職能部門,或者處于哪個層級的職位,都必須嚴(yán)格遵循精確的流程。豐田體系的第一條潛規(guī)則就是,必須對每項作業(yè)活動詳加說明。
在豐田的工廠里,對于某一項工作,操作工(不論新老,也不論普通員工還是主管)都遵循著一套嚴(yán)格規(guī)定的步驟。如果稍微偏離操作規(guī)程,問題就會立即顯露出來。由于能夠立即發(fā)現(xiàn)偏差,所以能馬上采取行動,糾正錯誤,然后再決定如何修改流程規(guī)定,或者對犯錯的人進行再培訓(xùn),以防止差錯再次出現(xiàn)。即使是一些復(fù)雜的、不常見的活動,例如在新工廠培訓(xùn)非熟練工人、推出一個新車型、更換生產(chǎn)線,或者把設(shè)備從工廠的某個區(qū)域移至另一個區(qū)域等等,也是按照這條原則來設(shè)計的。
規(guī)則一要求工人們必須嚴(yán)格按照規(guī)定的步驟順序完成工作,這樣就迫使他們在行動中檢驗原始的假設(shè)。完成這項作業(yè)會對工作設(shè)計中的兩個隱含假設(shè)進行檢驗:第一,完成這項作業(yè)的人有正確執(zhí)行任務(wù)的能力;第二,完成這項作業(yè)確實會帶來預(yù)期結(jié)果。還記得安裝汽車座椅的工人嗎?如果他不能在規(guī)定的時間按照規(guī)定的方式把座椅安裝妥當(dāng),那么他顯然至少把兩個假設(shè)中的一個給推翻了,說明這項作業(yè)需要重新設(shè)計,或者這名工人需要重新培訓(xùn)。
規(guī)則二:明確的分工與暢通的流程
第一條規(guī)則闡述的是人們?nèi)绾瓮瓿筛髯缘淖鳂I(yè)活動,而第二條規(guī)則解釋了工人之間的工作銜接。規(guī)則二是指每個銜接環(huán)節(jié)都必須是規(guī)范化和直接的,必須毫不含糊地明確規(guī)定涉及的人員、提供的產(chǎn)品和服務(wù)的形式和數(shù)量、每個“客戶”提出需求的方式,以及滿足需求的預(yù)計時間等等。通過該規(guī)則,每個工人與負責(zé)為他提供特定貨物或服務(wù)的員工之間,就建立起一種客戶——供應(yīng)商關(guān)系。所以,在決定由何人、于何時、把何物提供給誰這個問題上,不存在任何灰色區(qū)域(gray zone)。當(dāng)某個工人要求得到零件時,誰應(yīng)當(dāng)來提供、要供應(yīng)多少數(shù)量以及何時交貨等等,這些都是明白無誤的。同樣,如果某人需要幫助,那么誰應(yīng)該提供幫助、從哪里開始幫助,以及提供哪些服務(wù)等等,也都是明白無誤的。
在豐田工廠中,諸如“看板”與“安燈”等其他裝置在供給者與需求者之間建立起直接聯(lián)系。由于有了深思熟慮的設(shè)計和不折不扣的執(zhí)行,所以這些銜接工作進行得很順暢,猶如奧運會上最出色的接力隊在傳遞接力棒一樣。
豐田要求在規(guī)定的時間內(nèi)對供貨需求做出響應(yīng),這進一步降低了產(chǎn)生差異的可能性。如果涉及服務(wù)方面的需求,更是如此。當(dāng)一名工人碰到問題時,他就應(yīng)當(dāng)立即求助,而指定的幫助者則應(yīng)當(dāng)立即做出回應(yīng),并且在那名工人的作業(yè)周期內(nèi)把問題解決。用這種方式保持了整個體系的柔性,使得系統(tǒng)的持續(xù)改善和建設(shè)性調(diào)整成為可能。
規(guī)則三:生產(chǎn)線無間斷流程
在豐田,構(gòu)筑任何一條生產(chǎn)線,都必須保證產(chǎn)品或者服務(wù)能夠沿著簡單、確定的路線流動,除非生產(chǎn)線需要重新設(shè)計,否則該路線不得輕易更改。原則上,在豐田的任何一條供應(yīng)鏈上,都不能有分岔或者回流等干擾正常流程的現(xiàn)象——這就是第三條規(guī)則。
按照第三條規(guī)則設(shè)計生產(chǎn)線的時候,關(guān)鍵在于貨物和服務(wù)并不是朝著任意一個有空暇的員工或機器流去,而是流向某個指定的員工或者機器。如果由于某種原因該員工或者機器不能及時處理,豐田就會將其視為一個問題,這意味著生產(chǎn)線需要重新設(shè)計。
然而,每個產(chǎn)品都必須按照簡單、既定的路線流動這條規(guī)定,并不意味著每條路線只能由一種產(chǎn)品專用。恰恰相反,豐田工廠里的每一條生產(chǎn)線都適用于多種產(chǎn)品類型,通常比其他公司生產(chǎn)線上適用的品種要多得多。
第三條規(guī)則不僅適用于產(chǎn)品,也適用于服務(wù),如對求助的回應(yīng)等。舉例來說,如果座椅安裝工需要幫助,那么提供幫助的也必須是指定人員。如果該人員不能提供必要的幫助,那么他又會向自己的指定幫助者求助。在豐田的某些工廠里,這樣的援助線路可能包括3個、4個或者5個環(huán)節(jié),涉及人員從基層的車間工人一直到高層的工廠經(jīng)理。
第三條規(guī)則要求所有的線路必須得到明確規(guī)定,從而保證線路的每次使用都相當(dāng)于一次實驗。根據(jù)第三條規(guī)則所設(shè)計的線路包含著兩個假設(shè):所有與該線路有關(guān)聯(lián)的供應(yīng)者都是必需的,而任何未與該線路建立關(guān)聯(lián)的供應(yīng)者都不是必需的。假如汽車零件供應(yīng)企業(yè)的工人們希望轉(zhuǎn)向另一臺機器或者焊臺進行生產(chǎn),或者轉(zhuǎn)向非指定的幫助者求助,那么他們就可以下結(jié)論:自己的實際需求或?qū)嶋H能力與自己的初始預(yù)期并不相符。此外,對于應(yīng)該使用哪臺壓力機或者焊機,也不應(yīng)含糊不清。所以,這意味著工人們有必要重新審查生產(chǎn)線的設(shè)計。就像規(guī)則一和規(guī)則二那樣,規(guī)則三能夠使豐田開展實驗,同時又保持了柔性和響應(yīng)度。
規(guī)則四:持續(xù)改進
發(fā)現(xiàn)問題只是第一步。要持續(xù)有效地變革,人們必須知道如何變革以及誰應(yīng)該負責(zé)變革。豐田明確地指導(dǎo)員工如何進行改進,而不是指望他們單憑個人經(jīng)歷獲得教益。于是,就有了第四條規(guī)則。具體而言,規(guī)則四規(guī)定:對生產(chǎn)作業(yè)、工人或者機器之間的工作銜接以及流程路線所做的任何改進,都必須按照科學(xué)的方法,在老師的指導(dǎo)下,在盡可能低的組織架構(gòu)層面施行。
二、矛盾推動精益發(fā)展
以下的觀點主要參考《The Contradictions That Drive Toyota's Success》。
精益生產(chǎn)是豐田的“硬件”創(chuàng)新,使公司能夠不斷改進汽車制造方式,降低制造成本,而真正推動豐田不斷成功的, 是豐田的“軟件”創(chuàng)新,即豐田精益生產(chǎn)背后的促使豐田不斷改進的精益思想。精益思想在豐田營造了許多矛盾與悖論,這些交錯的矛盾使得員工不斷挑戰(zhàn)新的困難,創(chuàng)新、超越。豐田今時今日的偉大成功來源于“軟硬”的協(xié)同。
豐田不認(rèn)為效率就能夠保障成功,毫無疑問,沒有一家企業(yè)將泰勒的標(biāo)準(zhǔn)化作業(yè)發(fā)揮會得像豐田一樣如此淋漓盡致。豐田與很大企業(yè)最大的不同在于,它不僅僅把員工看作是機械的一部分,而把他們看作是蘊藏知識的知識型人才,他們都是具有豐富一線經(jīng)驗的智慧代表。因此,豐田注重員工與組織能力的投資,贏得來自世界各地的每位員工的想法,不論是車間,還是辦公室。人類認(rèn)識的研究表明,如果人們面對非常矛盾的想法的時候,他們會給予了一個問題不同方面的見解,并且會促使有效的解決辦法產(chǎn)生。因此豐田有意在組織中培養(yǎng)各種各樣的矛盾的觀點,促使員工接受挑戰(zhàn),找到適合的解決方法。尋找不同,而不是達成一致,這種文化促進了豐田不斷產(chǎn)生創(chuàng)新的思維,這也是它領(lǐng)先對手的根本原因。
對于許多西方人來說,大多數(shù)人覺得豐田深不可測,因為它沒有表現(xiàn)出任何企業(yè)成功的標(biāo)志。事實上,它類似于一個失敗或停滯不前的巨頭企業(yè)。例如豐田支付相對較低的紅利和薪酬,很多人認(rèn)為這是效率低下的表現(xiàn)。從1995年到2006年,豐田的紅利平均只有利潤的20 %。2006年支付的21.3 %是在標(biāo)準(zhǔn)桿與規(guī)模較小的競爭對手相比,如日產(chǎn)的22.9 %和現(xiàn)代的17.4 % ,但遠遠落后(當(dāng)時)戴姆勒克萊斯勒47.5 % 。與此同時,它積累了200億美元的現(xiàn)金,很多人士將其稱為豐田銀行。豐田的矛盾表現(xiàn)如下:
豐田動作緩慢,但它飛躍
例如,豐田涉足美國的汽車市場比任何對手都要晚。1984年,豐田才與通用在加利福尼亞州組建合資企業(yè)New United Motor Manufacturing,四年之后在肯塔基州開設(shè)了第一家工廠。然而,1997年在日本推出的普銳斯,這是一個巨大的飛躍。比所有競爭對手都要早,豐田設(shè)計了混合動力發(fā)動機,結(jié)合了內(nèi)燃機與環(huán)保的電動馬達。
豐田穩(wěn)步增長,但它是一個偏執(zhí)的公司
在20世紀(jì)50年代初,豐田曾經(jīng)瀕臨著破產(chǎn),但在50年之后的幾十年中,豐田已經(jīng)取得了穩(wěn)定的銷售和市場份額的增長。盡管這個令人羨慕的穩(wěn)定增長的情況下,高級管理人員仍然不斷傳播豐田的信念,如“永不滿足”和“有必須有一個更好的辦法”,例如奧田碩最愛說的是“好的時候也需要改革”,渡邊喜歡指出“沒有變化是一件壞事”。
豐田的運營是有效的,但它似乎在浪費員工的時間
你會驚訝地看到有多少人參加豐田的一次會議,即使其中大部分人是不參加討論。豐田外派的員工人數(shù)超過競爭對手,而且其高級管理人員花費很多的時間拜訪的經(jīng)銷商。豐田還雇用了大量的多語種協(xié)調(diào)員,以幫助打破日本總部和國際業(yè)務(wù)之間的障礙。
豐田儉樸,但它在關(guān)鍵領(lǐng)域投資龐大
當(dāng)今世界上,或許只有沃爾瑪?shù)墓?jié)省每一份錢的低成本戰(zhàn)略可以與豐田的低成本相較量。在日本,在午飯時間關(guān)閉燈光。由于在日本辦公空間成本很高,工作人員往往在一個大房間共同工作,沒有辦公桌之間的分割。與此同時,豐田花費大量資金建設(shè)生產(chǎn)設(shè)施、完善經(jīng)銷商網(wǎng)絡(luò)和開發(fā)人力資源。例如,自1990年以來,它已經(jīng)在美國與歐洲的生產(chǎn)中心與輔助設(shè)備投資220億美元,并在過去六年里,它每年在F1比賽中投入1.7億美元。
豐田堅持簡單的內(nèi)部溝通,但它的社會網(wǎng)絡(luò)基礎(chǔ)復(fù)雜
一條不成文的規(guī)則,豐田的員工互相溝通時必須保持簡單的語言。在做總結(jié)匯報的時候,他們必須單頁紙內(nèi)總結(jié)背景資料、目標(biāo)、分析、行動計劃和預(yù)期的結(jié)果。與此同時,豐田助長了復(fù)雜的社會網(wǎng)絡(luò),因為它要“每個人都知道一切。”該公司開發(fā)了跨職能跨地域員工之間的橫向聯(lián)系系統(tǒng);通過教學(xué)關(guān)系和指導(dǎo)創(chuàng)建科層制的垂直溝通;促進非正式聯(lián)系,邀請員工加入老鄉(xiāng)、體育、愛好等俱樂部等等。豐田雖然有嚴(yán)格的等級制度,但它又給了員的充分的授權(quán)。
提出反向意見,揭露問題,而不是盲目遵守老板的命令-這是所有員工的允許行為。我們會驚訝地聽到員工在豐田批評公司和高級管理,但員工似乎并不擔(dān)心。因為他們所做的是做正確的事情,給主管提供建設(shè)性的批評。
一旦我們認(rèn)識到,豐田的成功是這些矛盾,試圖找出協(xié)調(diào)矛盾潛在的力量。我們就會像剝洋蔥一樣:一層又一層,似乎從來沒有進入中心。終于最后,發(fā)現(xiàn)有四股力量促使豐田的發(fā)展和改善。這些矛盾使組織更加多樣化,決策更加復(fù)雜,并威脅企業(yè)對于溝通的控制。所以,為了防止這些矛盾動搖了豐田,豐田利用這四股力量的整合穩(wěn)定,幫助員工合理的運作,并延續(xù)豐田的價值觀和文化。這四股力量就是,新思想的力量、設(shè)置模糊和不可能的目標(biāo)、當(dāng)?shù)囟ㄖ坪蛯嶒灐?/p>
新思想的力量
“這是我們在這里做事情的方式”這是一種在組織中常見的限制思維的想法。慣例成為標(biāo)準(zhǔn)和創(chuàng)造效益。但隨著時間的推移,這些方法可以阻礙新的想法產(chǎn)生。豐田防止僵化的爬行,促使員工思考如何吸引新客戶,新市場和新的地理區(qū)域和如何用新思路,新做法應(yīng)對競爭對手的挑戰(zhàn)。
模糊和不可能的目標(biāo)
許多豐田的目標(biāo)含糊不清,允許他們的員工將他們的精力投向不同的方向,并促使不同職能領(lǐng)域的專業(yè)人士協(xié)作共同協(xié)作。例如,渡邊說,他的目標(biāo)是建立一個汽車,可以不污染空氣,可以防止意外事故,當(dāng)人們啟動它的時候使人們健康和幸福,并帶給您從海岸到海岸的清新空氣。Zenji Yasuda,前豐田汽車高級董事經(jīng)理指出,“如果目標(biāo)更具體,雇員將無法發(fā)揮其全部潛力。模糊的目標(biāo)賦予研究人員開辟新領(lǐng)域的自由;尋找擁有這樣技術(shù)的未知的新供應(yīng)商;考慮下一個步驟需如何出售此類產(chǎn)品”。
通過設(shè)置近期無法實現(xiàn)的目標(biāo),豐田的高級管理人員使得公司擺脫了既定程序。這種做法可以追溯到豐田的創(chuàng)始。1937年,創(chuàng)始人豐田喜一郎,在日本沒有技術(shù)的情況下希望依靠自己、不接受外國投資,生產(chǎn)日本自己的汽車。這看起來似乎是不可能實現(xiàn)的目標(biāo),即使當(dāng)時強大的財閥,如三菱和三井已決定在當(dāng)時的階段不進入汽車業(yè),因為他們不想作出如此遙遙無期的投資。然而豐田敢于創(chuàng)造歷史。
當(dāng)?shù)囟ㄖ?/p>
豐田不僅僅在產(chǎn)品設(shè)計上滿足當(dāng)?shù)匦枨?,而且企業(yè)的運營適合當(dāng)?shù)匚幕c水平。這一戰(zhàn)略推動了豐田汽車從日本走出來,并進入以前是其劣勢的海外市場。執(zhí)行本土化策略增加業(yè)了務(wù)的復(fù)雜性,但它最大程度地提高了員工的創(chuàng)造性,因為員工必須開發(fā)新技術(shù),新市場營銷方法和新的供應(yīng)鏈。日產(chǎn)和本田遵循同樣的策略,但他們?nèi)狈?yán)格的標(biāo)準(zhǔn):在2006年,豐田提供94個型號-幾乎是日產(chǎn)與本田的三倍,日產(chǎn)3 5和本田3 0。推行地方定制也使豐田察覺當(dāng)?shù)氐目谖?。例如?999年當(dāng)它引進了微型小型Yaris,豐田不得不提供先進的技術(shù),更安全、寬敞的內(nèi)部,以及更好的燃油效率,不辜負歐洲顧客的期望。
當(dāng)?shù)囟ㄖ剖沟秘S田不得不運用不同方式滿足客戶。例如,在1998年豐田面臨著復(fù)雜的挑戰(zhàn)時,豐田開發(fā)了創(chuàng)新國際多用途車(IMV)平臺。豐田工程師們設(shè)計滿足140多個國家的消費者需要的制造平臺,這些消費者來自亞洲,歐洲,非洲,大洋洲,中美洲和南美洲以及中東地區(qū)。IMV主要用于三個類型汽車的生產(chǎn)-卡車,微型面包車和運動型多用途車-豐田可以最大限度地降低設(shè)計和生產(chǎn)成本。值得注意的是,IMV生產(chǎn)線的汽車豐田首先在海外生產(chǎn),而不是首先在日本生產(chǎn),這形成了分散發(fā)展的生產(chǎn)訣竅,制造技術(shù),生產(chǎn)規(guī)劃和技術(shù)。自2004年以來,IMV模式在泰國,印尼,阿根廷,南非,印度,菲律賓和馬來西亞制造了自己的市場。IMV使豐田品牌與日本制造概念已經(jīng)無關(guān)了。許多管理人員認(rèn)為放棄這個標(biāo)簽是危險的,因為它已成為高質(zhì)量的代名詞。然而,負責(zé)銷售和亞洲生產(chǎn)執(zhí)行副總裁豐田昭夫,發(fā)起了一項個人運動,說服員工應(yīng)該用豐田制造取代日本制造。
實驗
豐田對于實驗渴望有助于清除阻礙實現(xiàn)近乎不可能的目標(biāo)障礙。通過鼓勵員工進行實驗,豐田走出舒適的區(qū)域,并進入未知領(lǐng)域。
豐田發(fā)現(xiàn),實現(xiàn)不可能目標(biāo)的切實可行的方式是要深入思考、小步前進、并永不放棄。它首先將一個大目標(biāo)分解到管理層級。然后,實驗,拿出新的舉措和流程處理每個挑戰(zhàn)。這種務(wù)實的做法通過創(chuàng)新帶來了許多學(xué)習(xí)機會。例如普銳斯德開發(fā)過程。在1993年,該公司決定開發(fā)一個環(huán)保和易于使用的汽車。這個開發(fā)小組便是21世紀(jì)汽車開發(fā)小組,首先提交了一個方案,提高50 %的燃油效率。豐田的高層管理人員拒絕了這個原型,并要求做100 %的改善。這是無法用時顯得,即使是最先進的汽油和柴油發(fā)動機,甚至燃料電池技術(shù)。21世紀(jì)汽車開發(fā)小組別無選擇,只能利用交叉技術(shù)。果然,首臺發(fā)動機無法啟動。隨后的模型只能移動幾百米的。盡管有這些挫折,豐田并沒有停止工作,終于在1995年東京汽車展推出了混合動力概念車。它的管理人員知道,混合動力技術(shù)是新興的,普銳斯不會停止他們前進的腳步。豐田認(rèn)為這個項目是值得的投資,豐田將學(xué)到很多東西的過程中。
眾所周知的,豐田的實驗程序嚴(yán)格。它是在完善計劃-嘗試-檢查-執(zhí)行( PDCA循環(huán))基礎(chǔ)上產(chǎn)生的 ,不斷改善的進程被應(yīng)用于整個商業(yè)世界。豐田業(yè)務(wù)流程的八個步驟制定了一個員工挑戰(zhàn)工作的路徑現(xiàn)狀:澄清問題;打破問題;設(shè)定目標(biāo);分析根源;制定對策;通過對策;監(jiān)測結(jié)果和過程;規(guī)范成功過程。
建立生產(chǎn)有序、管理順暢,操作規(guī)范,士氣高昂、高質(zhì)量、低成本、短交期的作業(yè)現(xiàn)場;
為企業(yè)規(guī)劃設(shè)計一套由內(nèi)到外的形象升級,外觀視覺價值體現(xiàn)、內(nèi)在的管理內(nèi)涵體現(xiàn);
全員參與設(shè)備管理高產(chǎn)出和低成本運營,提升設(shè)備管理能力,維護能力,提高效率
構(gòu)建班組生產(chǎn)管理體系、循環(huán)評價、人才育成、持續(xù)改善、績效管理、文化養(yǎng)成體系;
提高產(chǎn)品質(zhì)量、降低生產(chǎn)成本、縮短交期、增加利潤,讓管理更系統(tǒng)科學(xué),執(zhí)行力更強
對工廠的各個組成部分進行合理安排,以提高生產(chǎn)效率、降低成本、優(yōu)化物流、改善工作環(huán)境等